From magnificent bridges to intricate electronic components, welding technology is ubiquitous. With the continuous advancement of technology, welding methods are also constantly innovating. Laser welding, as an emerging high-energy beam welding technology, has gradually emerged in various fields due to its high precision, high efficiency, and low deformation, posing a significant challenge to traditional welding methods.
This article will discuss the comparison between laser welding and traditional welding methods, providing a detailed explanation from various perspectives such as working principles, advantages and disadvantages, and application scopes. This will help you gain a more comprehensive understanding of the advantages and limitations of laser welding and other welding methods, providing a reference for selecting the appropriate welding method for different industries.
How does Laser Welding Work?
Laser welding utilizes a laser as a heat source to heat materials, causing them to melt and join together. Due to the laser’s excellent monochromaticity and directionality, it can be easily focused into a very fine spot with extremely high energy density within the spot. Therefore, the main characteristic of laser welding is the high depth-to-width ratio of the weld seam.
Laser welding can be performed in the atmosphere, and sometimes shielding gas is used based on processing requirements. Lasers can weld high-melting-point materials and, in some cases, can achieve dissimilar material welding.
With the development of industrial lasers, control technology, and machine tools, fiber laser welders are evolving towards being smaller, more compact, efficient, durable, and reliable. They are equipped with computers, rotatable lenses, multi-channel beam splitting, and fiber transmission to enhance operational flexibility and automation levels.
Advantages of Laser Welding
- Short laser irradiation time, and extremely fast welding process
This not only helps improve productivity but also prevents the welded material from oxidizing easily. The heat-affected zone is small, making it suitable for welding highly heat-sensitive transistor components. Laser welding produces no slag and doesn’t require the removal of oxide film from the workpiece. It can even weld through glass, making it particularly suitable for welding in miniature precision instruments.
- Welding of dissimilar materials
Lasers can weld not only the same type of metal materials but also dissimilar metal materials, and even metal and non-metal materials. For example, using ceramics as the base for integrated circuits is challenging with other welding methods due to the high melting point of ceramics and the inadvisability of applying pressure. However, laser welding makes this relatively easy. Of course, laser welding cannot weld all dissimilar materials.
- High degree of automation
Laser welding is easy to automate and intelligently control. Through CNC systems and robotic technology, high-precision and high-efficiency welding processes can be achieved, reducing manual intervention, improving productivity, and lowering labor costs.
What are the common welding methods? What are the differences between them?
Understanding the working principles and characteristics of traditional welding methods helps in comprehending the differences between laser welding and other welding methods, thus clarifying the suitable welding method for your needs.
Arc Welding
Arc welding utilizes the intense electric arc generated between an electrode and a metal workpiece as the heat source. The high temperature of the arc melts the electrode and the metal workpiece locally. The filler metal in the electrode also melts and enters the molten pool. After the molten pool cools and solidifies, it forms a weld seam connecting the electrode and the workpiece.
There are many types of arc welding, including SMAW (Shielded Metal Arc Welding), MIG welding (Metal Inert Gas Welding), TIG welding (Tungsten Inert Gas Welding), plasma arc welding, and submerged arc welding.
Laser Welding vs Arc Welding
- Laser welding uses a high-energy-density laser beam as the heat source, while arc welding uses the electric arc generated between the electrode and the workpiece. The laser beam’s energy is concentrated, resulting in low heat input, a narrow heat-affected zone, and minimal welding deformation, making it suitable for precision welding and thin sheet welding. In contrast, arc welding has high heat input, a naturally wider heat-affected zone, and larger welding deformation, making it suitable for welding large structural components.
- Laser welding has a much faster welding speed than arc welding, with higher precision and weld quality. Laser welding is a non-contact welding process that doesn’t require filler metal, and the welding process is fume-free and easy to automate. Arc welding requires filler metal, and the welding process generates fumes and arc radiation, causing some environmental pollution, and having a lower degree of automation.
- The cost of laser welding equipment is relatively high, limiting its application in certain fields. Arc welding equipment is low-cost and easy to operate, making it suitable for situations where welding quality and precision requirements are not high, and the structures are simple.
Brazing
Brazing is a process that joins workpieces using a filler metal with a lower melting point than the base materials. It involves heating the workpieces and filler metal to a temperature above the filler metal’s melting point but below the base materials’ melting point. The molten filler metal flows into the joint gap through capillary action, wetting the base material surfaces and undergoing atomic diffusion. Upon cooling and solidification, it forms a brazed joint connecting the workpieces.
Laser Welding vs Brazing
- Laser welding utilizes a high-energy-density laser beam to locally melt the workpiece, forming a molten pool that solidifies upon cooling to create a joint. Brazing, on the other hand, uses a filler metal with a lower melting point than the base materials. It is heated to melting and fills the joint gap through capillary action, solidifying upon cooling to form a joint. Therefore, laser welding involves direct melting and fusion of the base materials, resulting in high joint strength, close to the strength of the base materials. In contrast, the joint strength of brazing is relatively lower, limited by the strength of the filler metal.
- Laser welding is suitable for various metals and some non-metals, particularly for high-melting-point and refractory metals. Brazing is suitable for a variety of metal materials, especially for joining dissimilar metals, thin sheets, and precision parts.
- Laser welding is widely used in automotive, aerospace, electronics, medical devices, and other fields where high welding quality and precision are required. Brazing is widely used in refrigeration, air conditioning, instrumentation, jewelry, and other fields where joint strength requirements are not high but good sealing and electrical/thermal conductivity are needed.
Electron Beam Welding (EBW)
Electron beam welding is performed in a high vacuum environment. An electron gun emits an electron beam, which is accelerated by high voltage and focused by electromagnetic lenses. The beam bombards the workpiece surface, converting kinetic energy into thermal energy, causing the workpiece to locally melt and achieve welding.
Laser Welding vs EBW
- Laser welding uses a laser beam as the energy source and can be performed in the atmosphere or a shielding gas environment. EBW utilizes an accelerated electron beam in a high vacuum environment and must be carried out in a vacuum chamber. This gives laser welding an advantage in operational flexibility, while EBW has higher requirements for equipment and the operating environment.
- The energy density of EBW is generally higher than that of laser welding, enabling deeper penetration and narrower weld seams, making it particularly suitable for thick plate welding and joining high-melting-point materials. Laser welding has a relatively lower energy density, but its beam is easy to control and focus, making it suitable for precision welding and joining complex-shaped parts.
- Due to its high energy density, the heat-affected zone of EBW is smaller than that of laser welding, reducing welding deformation and residual stress. This is particularly important for welding heat-sensitive materials and precision parts.
- EBW is suitable for welding high-melting-point, high-strength, and easily oxidized materials, such as titanium alloys and high-temperature alloys. Laser welding has a wider range of applications, including various metals and some non-metallic materials.
- EBW equipment is more expensive and requires a vacuum system and other auxiliary equipment, while laser welding equipment is relatively cheaper. Therefore, EBW is mainly used in aerospace, nuclear industry, precision instruments, and other fields with extremely high welding quality requirements. Laser welding has a broader range of applications, including automotive, electronics, medical, and other industries.
Micro Welding
Microwelding is a precision joining technique that utilizes a high-energy-density heat source to achieve connections at a microscopic scale. Its working principle typically involves focusing the heat source (such as a laser beam, electric arc, or electron beam) into a spot size of micrometers or sub-millimeters, rapidly melting the local area of the workpiece to achieve material joining.
Laser Welding vs Micro Welding
- Micro-welding is mainly used for joining miniature parts and microstructures, typically involving dimensions in the micrometer or sub-micrometer range. Laser welding has a wider range of applications and can be used for welding from miniature parts to large structures.
- Micro welding usually has a higher welding speed, suitable for mass production. Laser welding is also fast, but for welding miniature parts, micro welding may be more efficient.
- Both micro welding and laser welding are suitable for a variety of metals and some non-metallic materials. However, microwelding may be more advantageous for joining some special materials (such as biomaterials and electronic components) due to its small heat-affected zone, which can avoid damage to material properties.
Resistance Welding
Resistance welding utilizes the resistance heat generated by the passage of current through the contact surfaces and adjacent areas of the workpieces as the heat source. Under pressure, it causes local melting of the workpieces to achieve joining. The main types of resistance welding include spot welding, seam welding, projection welding, butt welding, flash welding, and high-frequency welding.
Laser Welding vs Resistance Welding
- Laser welding utilizes a high-energy-density laser beam as the heat source, achieving non-contact welding. In contrast, resistance welding relies on the resistance heat generated by the passage of current through the workpiece, requiring direct contact with the workpiece. Therefore, laser welding is suitable for complex-shaped and hard-to-reach workpieces, while resistance welding is more suitable for simple-shaped workpieces like lap joints and butt joints.
- Laser welding offers precise control over heat input, resulting in a small heat-affected zone and minimal welding deformation. This makes it suitable for precision welding and welding heat-sensitive materials. Resistance welding, on the other hand, has a relatively higher heat input, a wider heat-affected zone, and larger welding deformation, making it suitable for situations where welding deformation is not a major concern.
- Laser welding has a faster welding speed and higher efficiency, making it suitable for mass production. Resistance welding has a relatively slower welding speed and is more suitable for small and medium-batch production. Laser welding equipment is more expensive and requires professional operators, while resistance welding equipment is less costly, easy to operate, and readily automatable.
- Laser welding is suitable for welding a variety of metals and some non-metallic materials, with a wide range of applications, including automotive, aerospace, electronics, and medical industries. Resistance welding is mainly suitable for electrically conductive metal materials, such as steel and aluminum, and is widely used in automotive, home appliances, and construction industries.
How to Choose the Right Welding Method?
Welding, as an indispensable joining technology, plays a crucial role in various industries. However, with the wide variety of welding methods available in the market, choosing the most suitable welding technology for your industry’s needs has become a challenge for many companies. Next, we will explore how to choose the most appropriate welding method for your industry from multiple perspectives.
- Workpiece Material and Thickness
Different welding methods are suitable for different materials and thicknesses. For example, laser welding is suitable for various metals and some non-metallic materials, and it particularly excels in thin sheet welding. In contrast, arc welding is more suitable for thick plate welding and large structural components. Therefore, when choosing a welding method, the first consideration should be the type and thickness of the workpiece material.
- Evaluate Welding Quality and Precision Requirements
Different industries have varying requirements for welding quality and precision. For instance, industries like aerospace and medical devices have extremely high demands for welding quality and precision, making laser welding and electron beam welding ideal choices. On the other hand, industries like construction and bridge building have relatively lower requirements for welding quality and precision, and traditional welding methods like arc welding and resistance welding can also meet their needs.
- Focus on Production Efficiency and Cost
The choice of welding method should also consider production efficiency and cost. Highly automated welding methods like laser welding and electron beam welding, although having higher equipment costs, offer high production efficiency and are suitable for mass production. Traditional welding methods like arc welding and resistance welding have lower equipment costs but relatively lower production efficiency, making them suitable for small and medium batch production or on-site welding.
- Consider Environmental Factors and Safety
Some welding methods generate fumes, harmful gases, or radiation during the welding process, which can impact the environment and the health of operators. Therefore, environmental factors and safety should also be considered when choosing a welding method. Laser welding and electron beam welding are relatively environmentally friendly, while arc welding requires attention to protective measures.
- Seek Professional Advice
If you are not familiar with welding technology or find it difficult to determine the most suitable welding method for your industry, you can seek professional advice. You can have detailed discussions with welding machine suppliers to learn more about welding expertise and let them provide you with professional guidance and suggestions. You can also inquire with friends who have purchased welding machines about their user experience.
Selection of Fiber Laser Welders
There are various types of fiber laser welding machines available in the market, such as handheld laser welding machines, tabletop laser welding machines, and automatic robot laser welders. Below is an introduction to different types of fiber laser welding machines, and you can choose based on your needs.
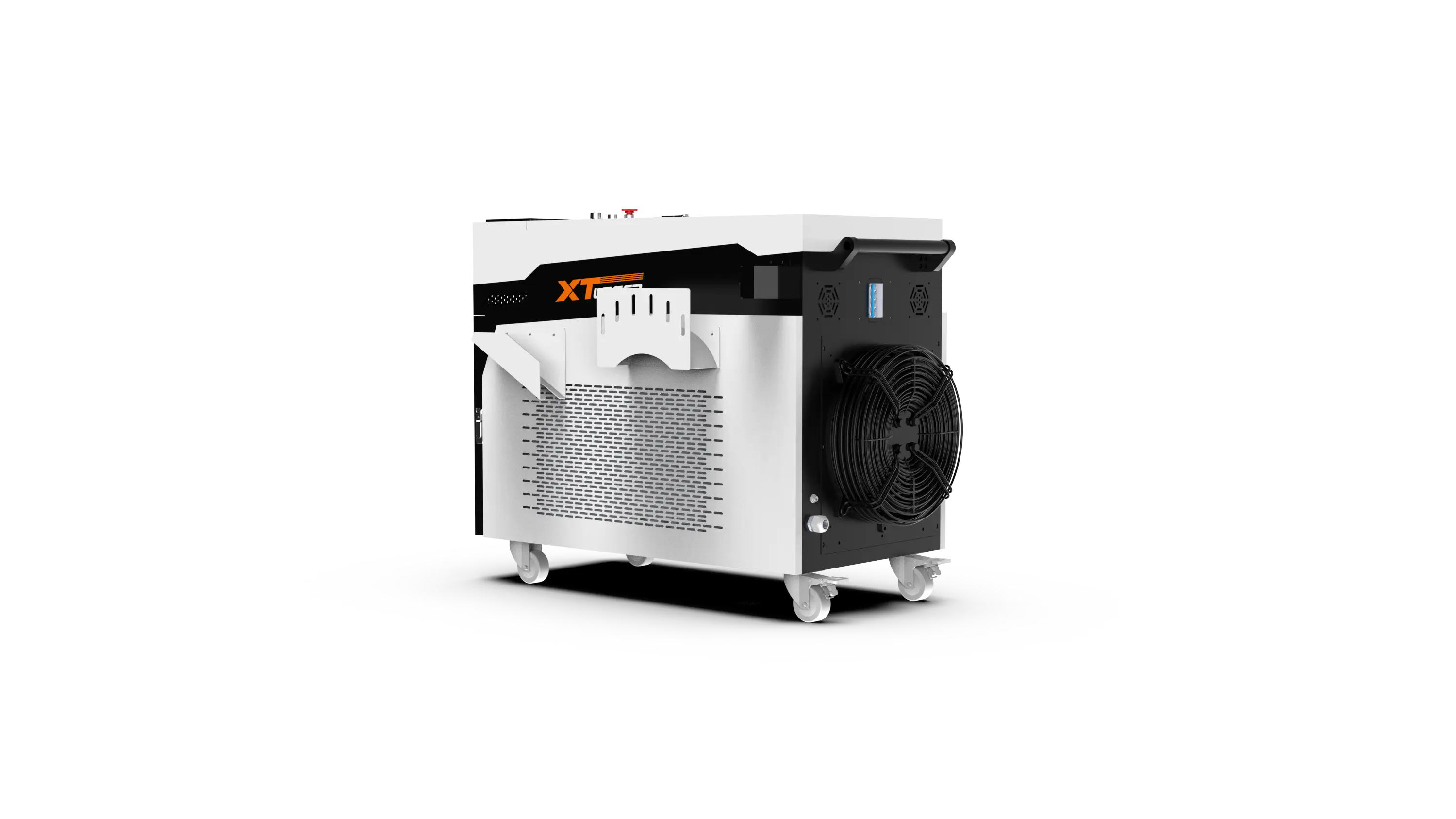
Handheld Laser Welding Machine
1000W/1500W/3000W options available; Spot/circle/line/8 other welding modes; Welding penetration depth 3mm/4mm/5mm

Tabletop Laser Welding Machine
1000W/1500W/3000W options available; Penetration depth (stainless steel) 2.8mm/4mm/5.2mm; Penetration depth (carbon steel) 2.7mm/4mm/5mm; Penetration depth (aluminum alloy) 2.2mm/3.3mm/4.2mm

Automatic Robot Laser Welder
1000W/1500W/3000W options available; Spot/circle/line/8 other welding modes
Conclusion
Through the comparative analysis of laser welding and traditional welding in this article, we can see the application characteristics of different welding methods in various fields. When choosing a welding method, we need to comprehensively consider factors such as workpiece material, welding requirements, production efficiency, and cost, weighing the advantages and disadvantages of laser welding and traditional welding methods to select the most suitable welding technology for our specific needs.
With the continuous development of laser technology and cost reduction, the application prospects of laser welding will become even broader. It is expected to play its unique advantages in more fields, driving the advancement of welding technology.