How to avoid the "burr" when cutting stainless steel with a laser cutting machine?
Stainless steel material has a beautiful surface, good rigidity and strength, corrosion resistance, easy to clean and other advantages, stainless steel products in the market in a very wide range of applications, and stainless steel laser cutting process is also widely used accordingly, laser cutting process has a fast cutting speed, good flexibility, processing capacity, cutting a wide range of advantages, but there are some process problems in the cutting process, the need for a corresponding solution to improve the Cutting effect. Next, XT LASER will take you to understand in detail!
Stainless steel laser cutting burr problem
CNC laser cutting machine for stainless steel with or without burrs is an important assessment criteria affecting the quality of laser cutting, because burrs not only affect the aesthetics of the cutting edge of the product, but also affect the use of the later, burrs require additional workload to remove.
Solution for burrs
- You need to check whether the laser energy output meets the requirements, in the stainless steel workpiece surface presents the spot is not round enough to ensure that the spot and the center hole of the nozzle to present the coaxial, the spot and the center hole of the nozzle the better the coaxiality, the better the quality of cutting. Round spot that is, after focusing through the lens formed after the spot energy distribution is uniform, the lateral distribution of laser energy is normal, in order to achieve qualified cutting quality;
- You should check whether there are fine particles, dust or splash residue and other debris on the lens and lens hardware of the laser transmission, which will also affect the presentation of the cutting quality, but also check whether there are small cracks in the laser lens, which are not easy to be found with the naked eye, but will also affect the transmission of laser energy.
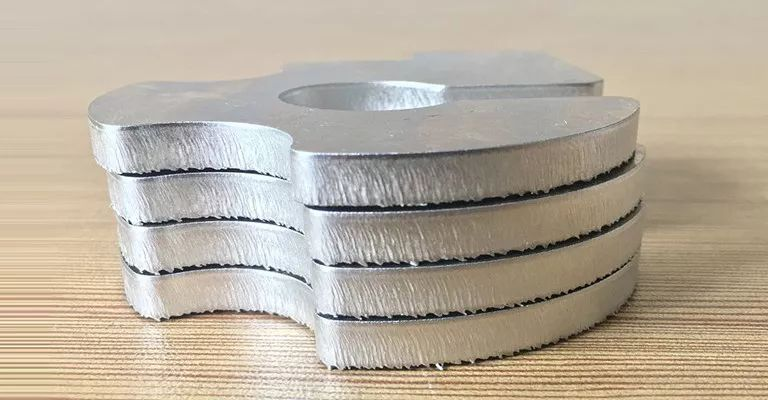
XT LASER as a professional stainless steel laser cutting machine manufacturer to remind the metal processing industry friends, stainless steel laser cutting burrs produced after the hardness is very large, not only after the removal of the sequence is very time-consuming and labor-intensive, but also affects the aesthetics of the workpiece. It is very necessary to solve the root cause, only first ensure that the above two points are checked normally, to determine whether the stainless steel laser cutting machine itself is normal, and only after that to further adjust the process parameter settings.
How to cut high quality thick plate stainless steel?
With the increasing development of the economy, people’s pursuit of quality of life is higher and higher, and everyone’s life is closely related to the use of stainless steel has also increased dramatically. Now laser cutting machine stainless steel thick plate process is more and more mature, will gradually replace the traditional cutting process. To cut high quality thick plate stainless steel, you need to fully understand the elements of the cutting process.
CNC laser cutting machine for stainless steel process elements are?
- Nozzle selection
The size of the nozzle diameter determines the shape of the gas flow into the cut, gas diffusion area, gas flow rate, thereby affecting the removal of molten material, cutting the stability of the situation. Into the mouth of the gas flow is large, fast, the workpiece in the gas flow in the right position, the ability to remove the melt jet the stronger. Fixed flow rate, different nozzle sizes, monitoring gas pressure the thicker the stainless steel, the selection of nozzles should be the larger the proportional valve is set to increase the flow rate, in order to ensure that the pressure, cut out the normal section effect.
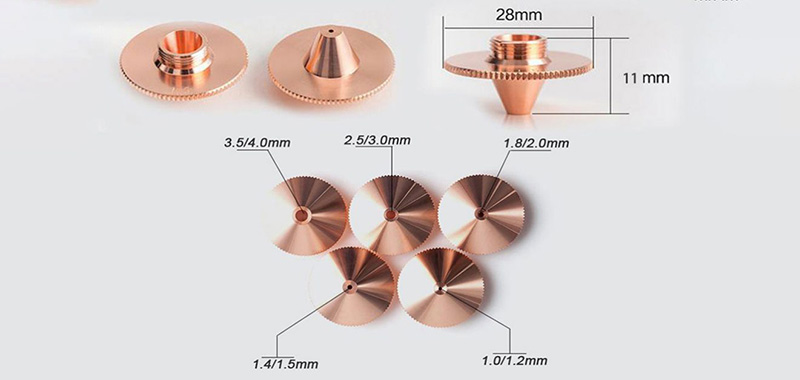
- Gas selection
Stainless steel laser cutting process often use a variety of auxiliary gases, such as oxygen, nitrogen, air, etc., the use of different types of gases, the effect of cutting section is different. Oxygen is black section, air is yellowish, nitrogen can keep the original color of stainless steel is not oxidized. Stainless steel cutting with nitrogen as the preferred auxiliary gas.
- [Oxygen] Advantages: high cutting speed, can cut thick sheet material purity recommendation: ≥99.999%
- [Nitrogen] Advantages: avoid the oxidation of the cutting edge, the workpiece therefore does not need to be re-processed Purity: ≥ 99.995% recommended
- Focus position
Laser cutting machine stainless steel is a beam of high energy density, so the focus spot diameter requirements to be small, in order to produce a narrow slit. Because the smaller the focal depth of the focusing lens, the smaller the focal spot diameter. For high quality cutting, the effective depth of focus is also related to the lens diameter and the material being cut. It is therefore important to control the position of the focal spot relative to the surface of the material being cut.
Since the laser power density has a great influence on the cutting speed, the choice of the focal length of the lens is an important issue. Laser beam focus spot size and lens focal length is directly proportional to the beam by the short focal length lens focus spot size is very small, the focal point of the power density is very high, the material cutting is very favorable; but it has the disadvantage of a very short depth of focus, the adjustment margin is small, generally more suitable for high-speed cutting of thin materials. As the long focal length lens has a wider depth of focus, as long as it has sufficient power density, it is more suitable for cutting thick workpieces.
After determining what focal length lens to use, the relative position of the focal point and the surface of the workpiece is particularly important to ensure the quality of the cut. As the highest power density at the focal point, in most cases, the focal point position during cutting is just at the surface of the workpiece, or slightly below the surface. In the entire cutting process, to ensure that the focus and the relative position of the workpiece is a constant relative position is an important condition for obtaining stable cutting quality. Sometimes, the lens is not cooled well and heated during the work, thus causing changes in the focal length, which requires timely adjustment of the focus position.
When the focal point is in the best position, the cut seam is the smallest, the highest efficiency, choose the best cutting speed can obtain ideal cutting results. This is also a way to improve the quality of stainless steel plate cutting.
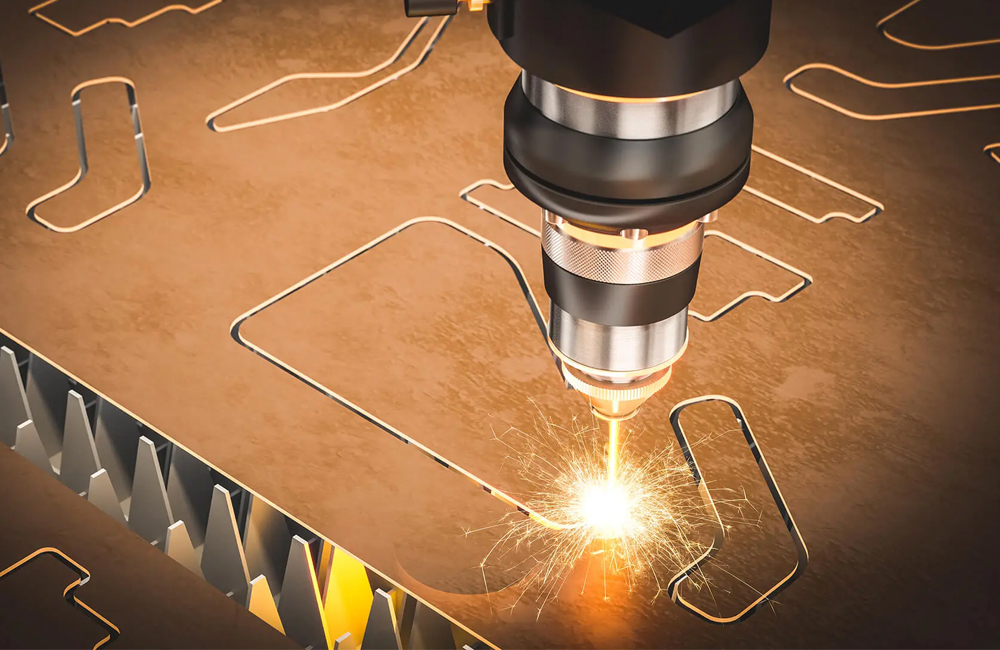
4. The laser frequency adjustment, as well as the duty cycle on the impact of cutting quality
- Frequency changes on the impact of stainless steel plate cutting:
Frequency from 500-200Hz range decreases, the cutting section effect becomes delicate, delamination slowly improve. When the frequency is set to 100Hz, it is impossible to cut and anti-blue light. Find out the optimum frequency range by changing the frequency. In order to ensure the best cutting section, it is necessary to ensure that the number of pulses is perfectly matched with the single pulse energy.
- The effect of duty cycle change on the cutting of thick stainless steel plate:
Duty cycle 53% is the critical value, continue to reduce the duty cycle, the lower surface of the appearance of uncut traces, the duty cycle increased to 60%, the section becomes rough, delamination is obvious, the cutting surface yellowing.
Precision work, in general, the height of the nozzle, machine movement parameters, movement acceleration, running speed, material and other impact on the cutting results also need to be tested and analyzed one by one, the need for laser process debugging technicians to actively work for the enhancement of the laser cutting process to make contributions. When the laser cutting capacity reaches 130 millimeters or even higher, the field of application will be further expanded.
Stainless steel laser cutting machine for sale
- Adopts plate welding bed, after high temperature annealing, high hardness, strong bearing capacity, corrosion resistance.
- Adopts high-power special intelligent cutting head, well-known brand motor, reducer, guide rail, rack, to provide reliable guarantee for the stable operation of stainless steel laser cutting machine.
- The processing area is set up with partition dust collection mode, which effectively shortens the air path travel and greatly improves the efficiency of extracting smoke and dust.
- The processing width of the equipment is very wide, and the table area can be customized according to processing needs.
Problems and solutions encountered in the laser cutting of stainless steel
1. Cutting slag
- If only the corner hanging slag, you can first consider the corner chamfering, parameters can be reduced focus, add atmospheric pressure and so on. If the whole hanging hard slag, you need to reduce the focus, add atmospheric pressure, increase the cutting nozzle, but the focus is too low or too much air pressure will lead to cross-section delamination and roughness.
- If the whole hanging granular soft slag, you can appropriately increase the cutting speed or reduce the cutting power. Cutting stainless steel is almost the end of the side hanging slag, check whether the gas supply gas flow can not keep up with the insufficient gas supply.
2. Cutting thin plate section is not bright enough, thick plate section is rough
- Want to cut the section of bright first of all have to plate good surface without rust, no paint, no oxide film, followed by oxygen purity should be high at least 99.5% or more, cutting needs to use a small nozzle double 1.0 or 1.2, cutting speed needs to be fast more than 2m/min, cutting air pressure should not be too large.
- Want to thick plate cutting section quality, first of all to ensure that the plate and gas purity, followed by the choice of nozzle,
- the larger the aperture section quality will be better, but at the same time the section taper will be larger.

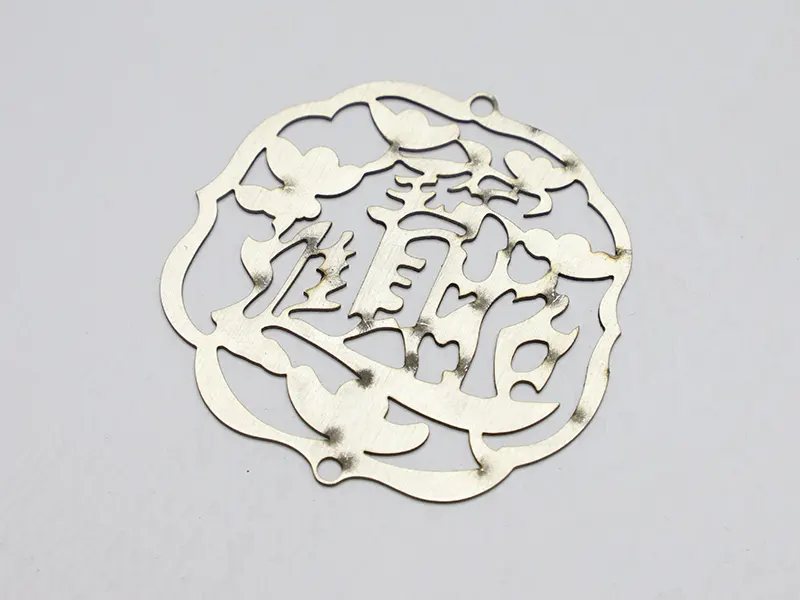
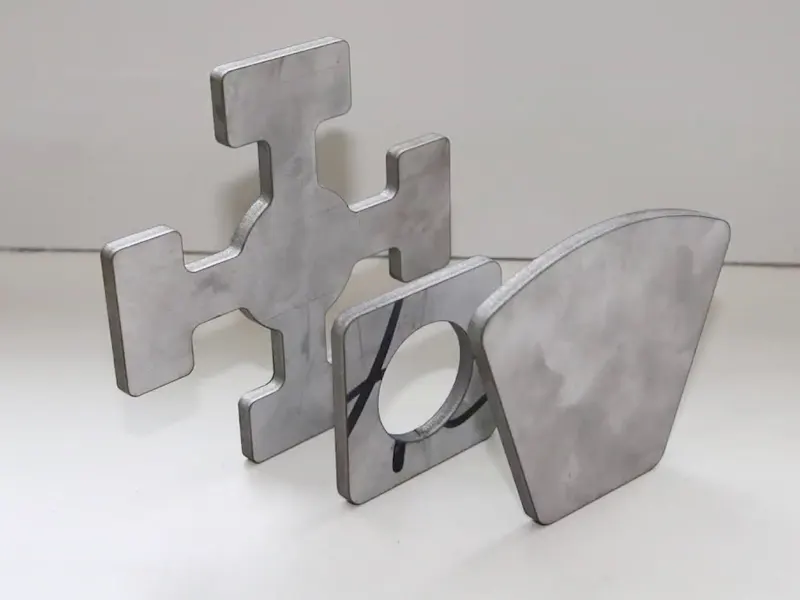
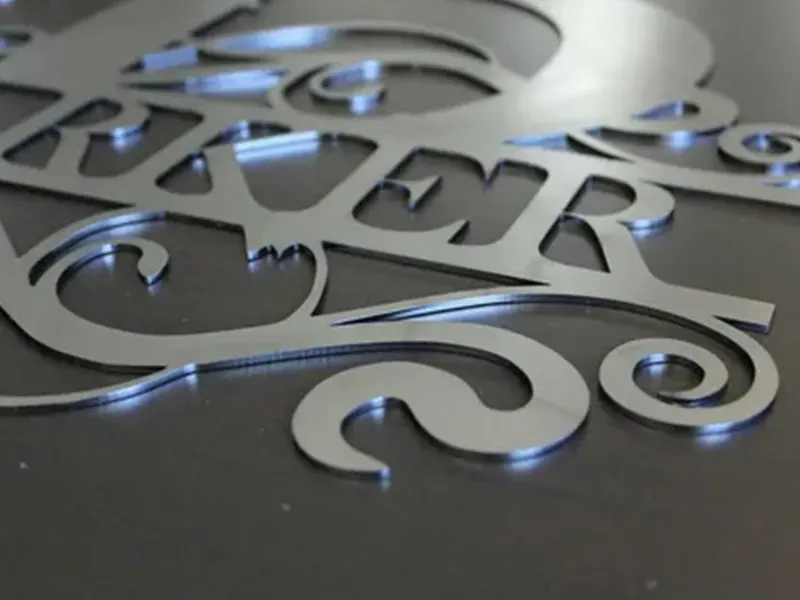