Поширені проблеми та шляхи їх вирішення в процесі лазерного різання
Лазерне різання - це високоточна, високоефективна технологія обробки, але в реальній експлуатації неминуче виникають деякі загальні проблеми. XT LASER детально проаналізує причини цих проблем і запропонує відповідні рішення, які допоможуть вам ефективно підвищити якість різання.
Нерівні ріжучі кромки або задирки
- Аналіз причин
① Недостатня потужність лазера: потужність занадто низька, матеріал не може бути повністю розплавлений, що призводить до нерівних країв різу.
② швидкість різання занадто висока: лазерний промінь не затримується на поверхні матеріалу на достатній проміжок часу, утворення задирки.
③ Неправильна фокусна відстань: положення фокусу лазера не точне, що впливає на якість різання.
Неправильний тиск газу: недостатній або високий тиск допоміжного газу призведе до утворення задирок.
Невідповідність властивостей матеріалу: параметри різання не налаштовані відповідно до типу і товщини матеріалу.
Забруднення лазерної головки: Бруд або кокс на лазерній голівці впливає на якість лазерного променя.
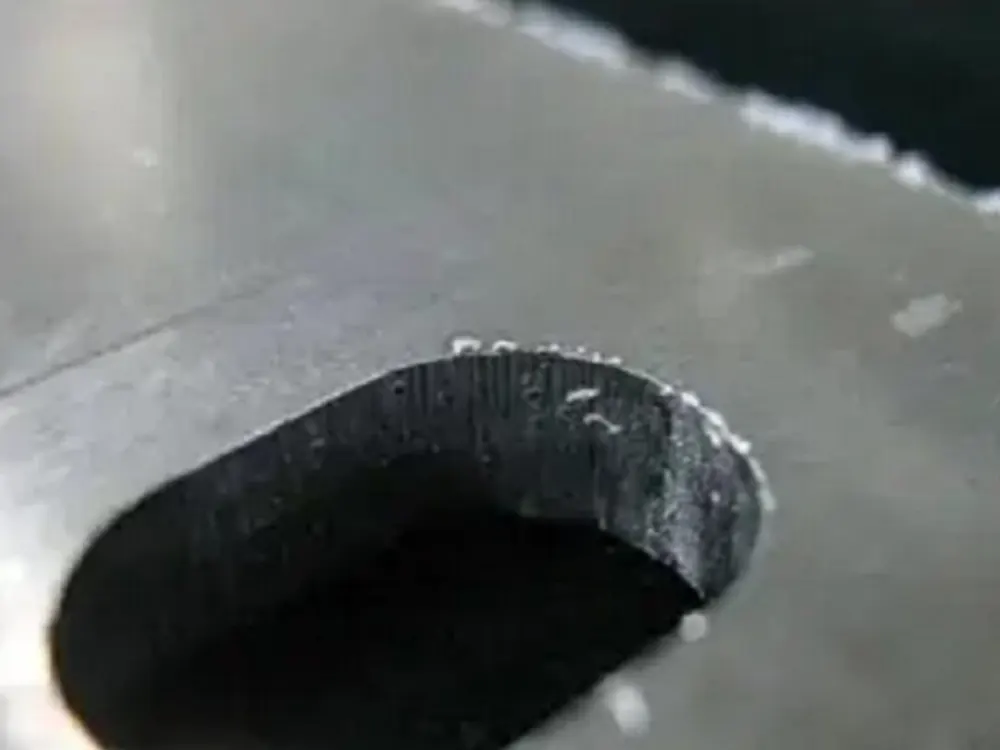
- Рішення:
① Відрегулюйте потужність лазера: Збільште потужність лазера відповідним чином.
① Відрегулюйте потужність лазера: Збільште потужність відповідним чином, щоб забезпечити повне розплавлення матеріалу.
② Оптимізуйте швидкість різання: Зменшіть швидкість, щоб лазер мав достатньо часу для завершення різання.
Відкалібруйте фокус: Переконайтеся, що фокус лазера є точним, а положення фокусу повинно бути на поверхні матеріалу або трохи нижче.
Відрегулюйте тиск газу: Відрегулюйте тиск допоміжного газу відповідно до характеристик матеріалу і переконайтеся, що швидкість потоку стабільна.
⑤ Вибирайте відповідні параметри: розумійте характеристики матеріалу та розумно встановлюйте потужність і швидкість різання.
⑥ Очищення лазерної головки: Регулярно чистіть лазерну головку, щоб підтримувати обладнання в належному стані.
Занадто широка ділянка різання або виникає явище плавлення
- Аналіз причин
① Занадто висока потужність лазера: налаштування потужності занадто високе, що призводить до надмірного розплавлення матеріалу.
② швидкість різання занадто низька: занадто низька, щоб лазер залишався занадто довго, збільшуючи зону термічного впливу.
Неточність фокусної відстані: неправильне розташування фокусної точки призводить до збільшення діаметра лазерного променя.
недостатній потік допоміжного газу: недостатній потік газу не може здути розплавлений метал, посилюючи явище плавлення.
⑤ Характеристики матеріалу не підходять: певні матеріали або матеріали з більшою товщиною мають більшу ймовірність розплавитися.
⑥ Погана якість лазерного променя: Погана рівномірність лазерного променя або кут розбіжності впливають на ефект різання.
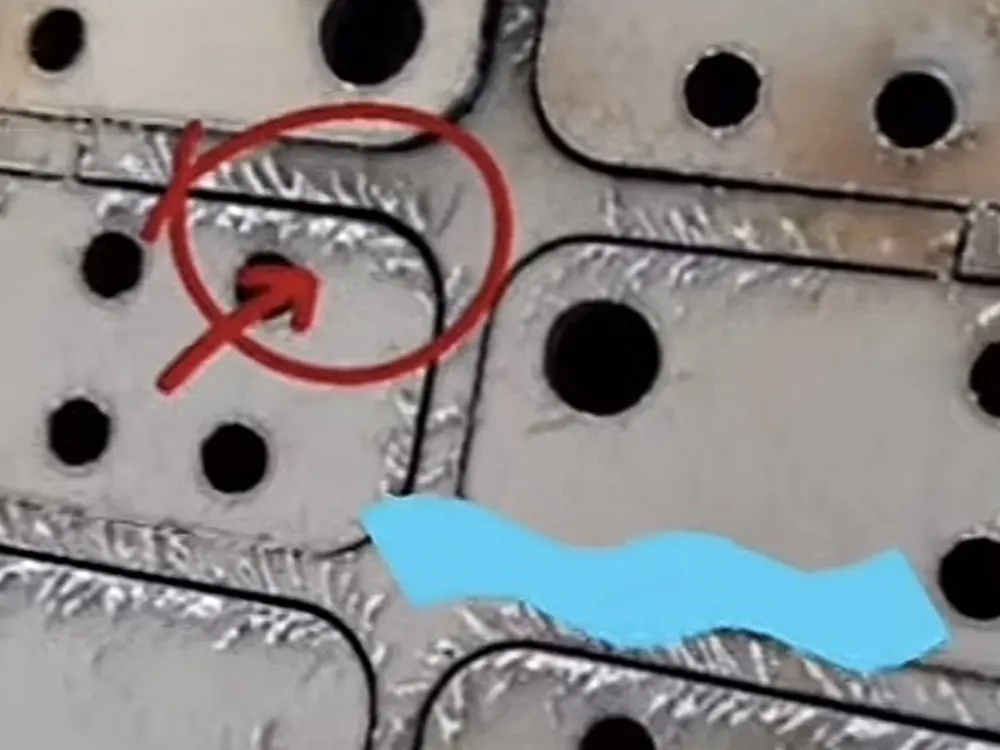
- Рішення
① Зменшити потужність лазера: відповідно до характеристик матеріалу відповідне зменшення потужності лазера.
② Збільшити швидкість різання: Відрегулюйте швидкість, щоб уникнути проблем з плавленням, спричинених занадто повільною роботою.
Відкалібруйте фокусну відстань: Переконайтеся, що положення фокусу лазера правильне.
Збільште потік допоміжного газу: Переконайтеся, що потік газу достатній для ефективного видування розплавленого металу.
⑤ Виберіть відповідний матеріал і параметри: Перед розпилюванням відрегулюйте параметри відповідно до характеристик матеріалу.
⑥ Покращити якість лазерного променя: Регулярно обслуговуйте лазерне обладнання, щоб забезпечити якість лазерного променя.
Поверхня різання не рівна і на ній є брижі
- Аналіз причин
① Коливання потужності лазера: нестабільна потужність лазера призводить до нерівномірного розподілу енергії.
швидкість різання нерівномірна: зміни швидкості впливають на час перебування лазерного променя на поверхні матеріалу.
Неточність фокусної відстані: неправильне розташування фокусної точки, погіршення якості різання.
деформація або нерівність матеріалу: деформація матеріалу або нерівність поверхні впливають на ефект різання.
Вібрація лазерної головки: недостатня механічна стабільність обладнання може спричинити вібрацію.
нестабільний потік допоміжного газу: нестабільний потік газу впливає на ефект видування розплавленого металу.

- Рішення
Стабілізація потужності лазера: Встановіть розумну максимальну та мінімальну потужність для забезпечення стабільної роботи лазера.
② Оптимізуйте швидкість різання: підтримуйте постійну швидкість та уникайте її коливань під час різання.
③ Відкалібруйте фокус: регулярно регулюйте положення фокусу лазера, щоб забезпечити точність різання.
④ Перевірте площинність матеріалу: вирівняйте матеріал перед різанням, щоб уникнути погіршення якості різання через викривлення.
⑤ Підвищити стабільність лазерної головки: Перевірте і затягніть механічні частини лазерної головки, щоб зменшити вібрацію.
⑥ Контролюйте потік газу: Переконайтеся, що потік допоміжного газу стабільний, щоб поліпшити якість поверхні різання.
Ненормальне іскріння під час різання
- Аналіз причин
Занадто висока потужність лазера: занадто високе налаштування потужності лазера може призвести до надмірного розплавлення матеріалу, генеруючи велику кількість іскор.
② занадто низька швидкість різання: занадто низька швидкість різання призведе до того, що лазер залишиться на матеріалі занадто довго, збільшуючи іскроутворення.
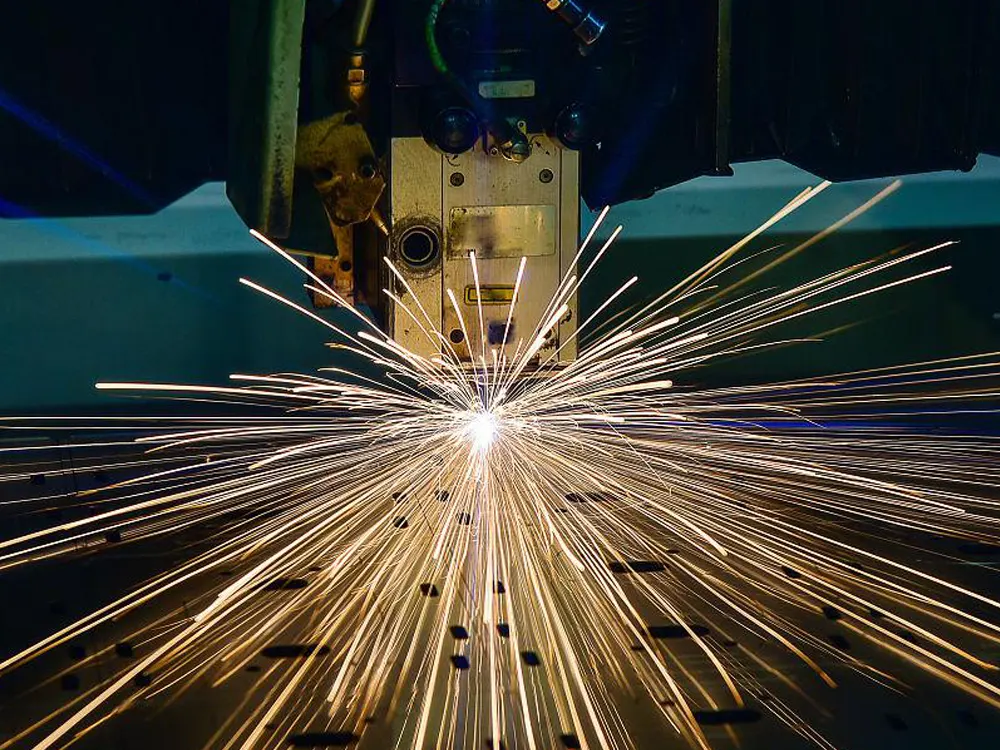
- Рішення
① Відрегулюйте потужність лазера: Зменшіть потужність лазера відповідно до товщини та типу матеріалу, щоб зменшити іскроутворення.
Оптимізуйте швидкість різання: збільште швидкість різання, щоб лазер впливав на матеріал протягом відповідного часу, щоб уникнути іскроутворення, спричиненого занадто повільною роботою.
Проблеми з якістю під час лазерного різання зазвичай виникають через налаштування параметрів, характеристики матеріалу або неналежне обслуговування обладнання. Регулюючи потужність, швидкість, фокусну відстань, оптимізуючи потік допоміжного газу тощо, можна ефективно покращити якість різання.