Lazer Kesim Sürecinde Sık Karşılaşılan Sorunlar ve Çözümleri
Lazer kesim yüksek hassasiyetli, yüksek verimli bir işleme teknolojisidir, ancak gerçek operasyonda kaçınılmaz olarak bazı yaygın sorunlarla karşılaşacaktır. XT LASER, bu sorunların nedenlerini ayrıntılı olarak analiz edecek ve kesim kalitesini etkili bir şekilde artırmanıza yardımcı olmak için ilgili çözümleri sağlayacaktır.
Pürüzlü kesme kenarları veya çapaklar
- Neden analizi
① Yetersiz lazer gücü: Güç çok düşüktür, malzeme tamamen eritilemez, bu da kaba kesme kenarlarına neden olur.
② kesme hızı çok yüksek: lazer ışını malzemenin yüzeyinde yeterli süre kalmıyor, lazer ışınının yüzeyinde çapaklar.
③ Odak uzaklığı doğru değil: lazer odak konumu doğru değil ve kesim kalitesini etkiliyor.
④ Uygun olmayan gaz basıncı: yardımcı gazın yetersiz veya yüksek basıncı çapak oluşumuna yol açacaktır.
⑤ Malzeme özelliklerinin uyumsuzluğu: kesme parametreleri malzemenin türüne ve kalınlığına göre ayarlanmamıştır.
⑥ Lazer kafası kirlenmesi: Lazer kafasındaki kir veya kok, lazer ışınının kalitesini etkiler.
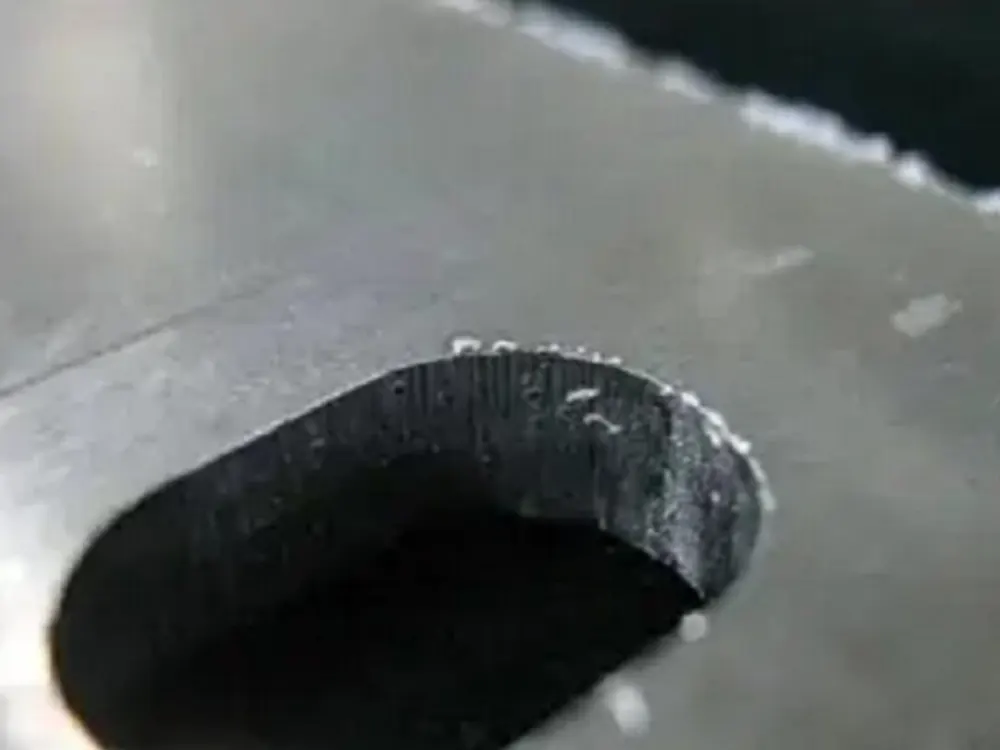
- Çözüm:
① Lazer gücünü ayarlayın: Lazer gücünü uygun şekilde artırın.
① Lazer gücünü ayarlayın: Malzemenin tamamen eridiğinden emin olmak için gücü uygun şekilde artırın.
② Kesme hızını optimize edin: Lazerin kesimi bitirmek için yeterli zamana sahip olması için hızı azaltın.
③ Odağı kalibre edin: Lazer odağının doğru olduğundan ve odak konumunun malzeme yüzeyinin üzerinde veya biraz altında olması gerektiğinden emin olun.
④ Gaz basıncını ayarlayın: Yardımcı gaz basıncını malzeme özelliklerine göre ayarlayın ve akış hızının sabit olduğundan emin olun.
⑤ Uygun parametreleri seçin: malzeme özelliklerini anlayın ve kesme gücünü ve hızını makul bir şekilde ayarlayın.
⑥ Lazer kafasını temizleyin: Ekipmanı iyi durumda tutmak için lazer kafasını düzenli olarak temizleyin.
Kesme bölümü çok geniş veya erime olayı meydana geliyor
- Neden analizi
① Lazer gücü çok yüksek: Güç ayarı çok yüksek, bu da malzemenin aşırı erimesine neden oluyor.
② kesme hızı çok yavaş: lazerin çok uzun süre kalmasına neden olacak kadar yavaş, ısıdan etkilenen bölgeyi arttırıyor.
③ Odak uzaklığı yanlışlığı: lazer ışınının çapının artmasına neden olan odak noktasının yanlış konumu.
④ yetersiz yardımcı gaz akışı: yetersiz gaz akışı erimiş metali uzaklaştıramaz ve erime olayını daha da kötüleştirir.
⑤ Malzeme özellikleri uygun değildir: belirli malzemelerin veya daha kalın malzemelerin erime olasılığı daha yüksektir.
⑥ Kötü lazer ışını kalitesi: Zayıf lazer ışını homojenliği veya sapma açısı kesme etkisini etkileyecektir.
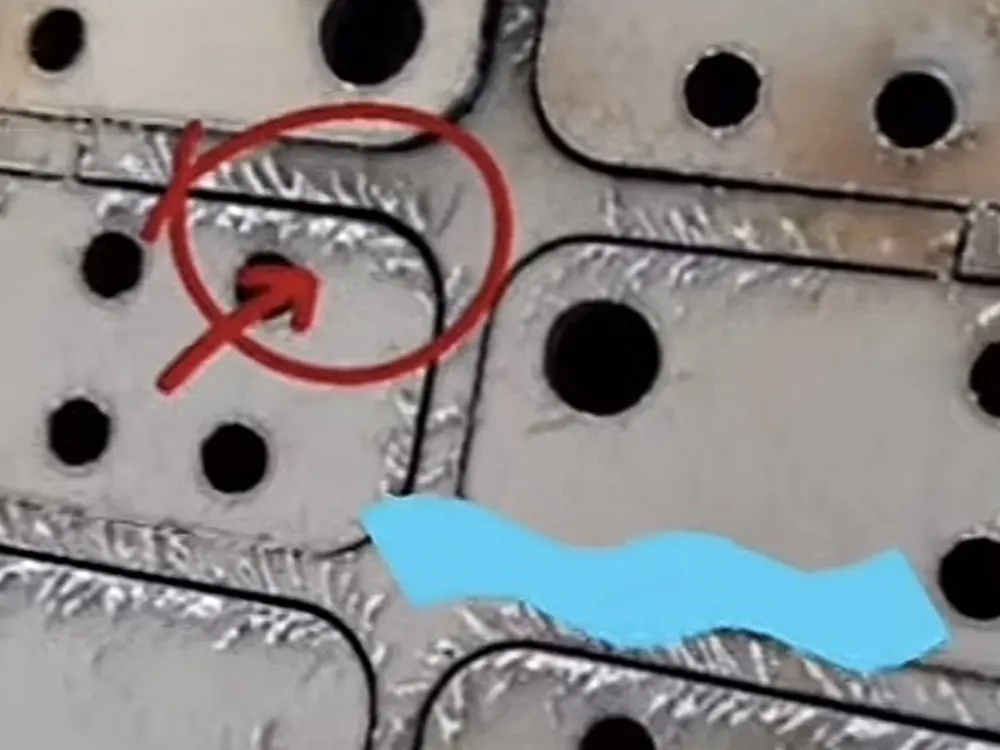
- Çözüm
① Lazer gücünü azaltın: malzeme özelliklerine göre lazer gücünün uygun şekilde azaltılması.
② Kesme hızını artırın: Çok yavaştan kaynaklanan erime sorunlarını önlemek için hızı ayarlayın.
Odak uzunluğunu kalibre edin: Lazer odak konumunun doğru olduğundan emin olun.
④ Yardımcı gaz akışını arttırın: Gaz akışının erimiş metali etkili bir şekilde uçurmak için yeterli olduğundan emin olun.
⑤ Uygun malzeme ve parametreleri seçin: Kesmeden önce, parametreleri malzeme özelliklerine uyacak şekilde makul olarak ayarlayın.
⑥ Lazer ışını kalitesini iyileştirin: Lazer ışını kalitesini sağlamak için lazer ekipmanının bakımını düzenli olarak yapın.
Kesme yüzeyi düz değil ve dalgalanmalar var
- Neden analizi
① Lazer gücü dalgalanması: dengesiz lazer çıkışı, eşit olmayan enerji dağılımına yol açar.
② kesme hızı tekdüze değildir: hız değişiklikleri malzeme yüzeyindeki lazer ışını süresini etkiler.
③ Odak uzaklığı yanlışlığı: odak noktasının yanlış konumlandırılması, kesim kalitesinin düşmesi.
④ malzeme deformasyonu veya düzgünsüzlüğü: malzeme eğriliği veya yüzey düzgünsüzlüğü kesme etkisini etkiler.
⑤ Lazer kafası titreşimi: ekipmanın mekanik stabilitesinin olmaması titreşime neden olabilir.
⑥ dengesiz yardımcı gaz akışı: dengesiz gaz akışı erimiş metalin üfleme etkisini etkiler.

- Çözüm
① Lazer gücünü stabilize edin: Stabil lazer çıkışı sağlamak için makul maksimum ve minimum gücü ayarlayın.
② Kesme hızını optimize edin: Hızı tutarlı tutun ve kesme sırasında hız dalgalanmasını önleyin.
③ Odağı kalibre edin: kesim doğruluğunu sağlamak için lazer odak konumunu düzenli olarak ayarlayın.
④ Malzeme düzlüğünü kontrol edin: eğilme nedeniyle kesim kalitesinin etkilenmesini önlemek için kesimden önce malzemeyi düzeltin.
⑤ Lazer kafası stabilitesini artırın: Titreşimi azaltmak için lazer kafasının mekanik parçalarını kontrol edin ve sıkın.
⑥ Gaz akışını kontrol edin: Kesme yüzeyinin kalitesini artırmak için yardımcı gaz akışının sabit olduğundan emin olun.
Kesme sırasında anormal kıvılcımlar
- Neden analizi
① Lazer gücü çok yüksek: Çok yüksek bir lazer gücü ayarı, malzemenin aşırı erimesine ve çok sayıda kıvılcım oluşmasına neden olabilir.
② kesme hızının çok yavaş olması: kesme hızının çok yavaş olması lazerin malzeme üzerinde çok uzun süre kalmasına neden olarak kıvılcım oluşumunu artıracaktır.
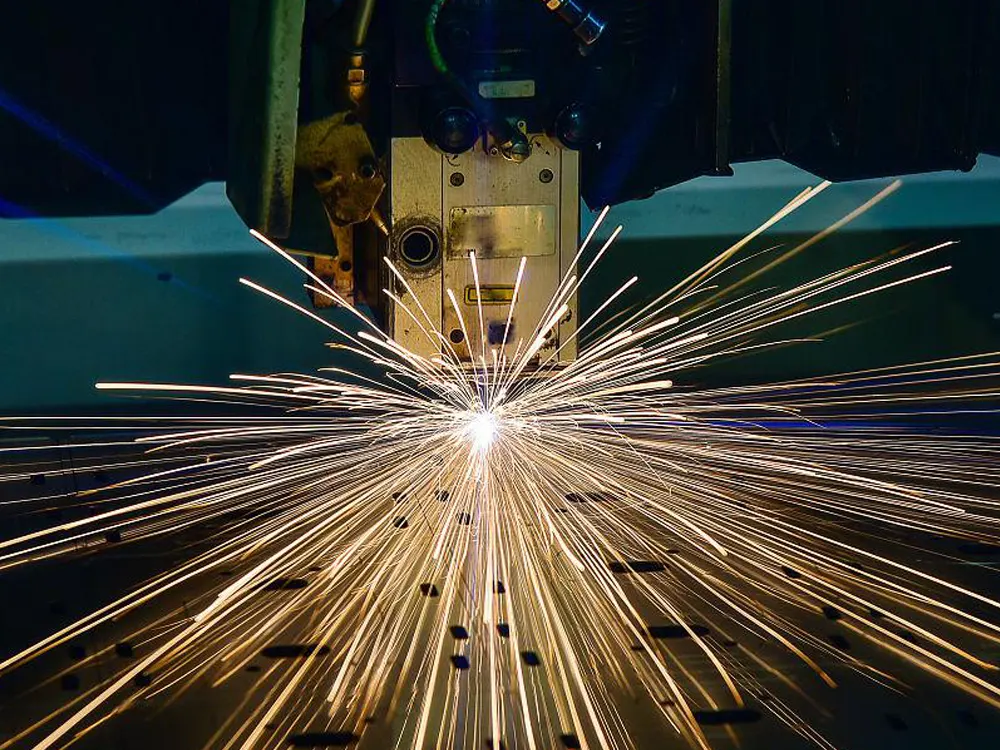
- Çözüm
① Lazer gücünü ayarlayın: Kıvılcım oluşumunu azaltmak için lazer gücünü malzemenin kalınlığına ve türüne göre uygun şekilde azaltın.
② Kesme hızını optimize edin: Lazerin malzemeye uygun süre boyunca etki etmesini sağlamak için kesme hızını artırın ve çok yavaşlamadan kaynaklanan kıvılcımları önleyin.
Lazer kesim sırasındaki kalite sorunları genellikle parametre ayarlarından, malzeme özelliklerinden veya yetersiz ekipman bakımından kaynaklanır. Güç, hız, odak uzaklığı ayarlanarak ve yardımcı gaz akışı optimize edilerek kesim kalitesi etkili bir şekilde iyileştirilebilir.