Saker att leta efter i en leverantör av laserskärmaskiner online
I den digitala tidsåldern är det mycket bekvämt att hitta en leverantör av laserskärmaskiner online, men det finns många utmaningar. Den här artikeln går igenom viktiga aspekter, från utvärderingsfaktorer till vanliga misstag som bör undvikas, och ger dig nödvändig kunskap för en lyckad upphandling.
Innehållsförteckning
5 saker du måste veta när du söker efter leverantörer av laserskärmaskiner på nätet
I dagens digitala tidsålder ger Internet oss stor bekvämlighet när vi köper laserskärmaskiner, och plattformar som Alibaba, eBay och olika branschspecifika webbplatser har blivit viktiga kanaler för oss att hitta leverantörer. Men inför ett brett utbud av leverantörer är det viktigt att lära sig hur man exakt utvärderar leverantörer. När du köper laserskärmaskiner finns det fem viktiga faktorer som du måste fokusera på.
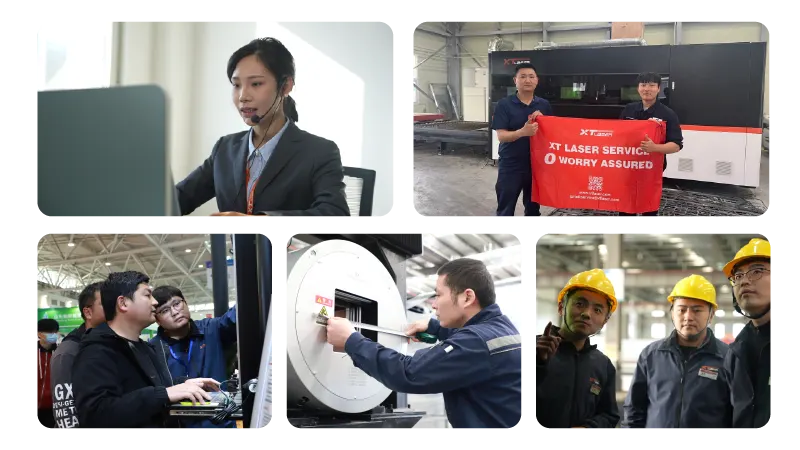
- Rykte och recensioner
Ryktet är grunden för en leverantör. När du söker efter leverantör av fiberlaserskärmaskin på plattformen, det första du bör göra är att kontrollera dess rykte på djupet. Kundrecensioner och återkopplingar är som en spegel som tydligt återspeglar leverantörens tillförlitlighet och produktkvalitet. Istället för att skumma igenom några recensioner och hoppa till slutsatser måste du vara tålmodig och leta efter konsekventa mönster i recensionerna. Om flera recensioner till exempel nämner frekventa produktfel, långsamma svar från kundservice etc., måste leverantören behandlas med försiktighet och undvika att välja en leverantör med för mycket negativ feedback för att undvika onödiga problem i framtiden. - Certifiering
Som en professionell utrustning måste säkerheten och kvaliteten på laserskärmaskinen uppfylla strikta industristandarder. Därför är det viktigt att se till att laserskärmaskinen som tillhandahålls av leverantören uppfyller relevanta certifieringar, som CE-certifiering, vilket indikerar att produkten uppfyller Europeiska unionens säkerhets-, hälso- och miljökrav; ISO9001-certifieringen återspeglar leverantörens standardisering i kvalitetsstyrningssystemet; och RoHS-certifieringen säkerställer att produkten uppfyller standarderna när det gäller begränsning av farliga ämnen. Att ha dessa certifieringar innebär att maskinen är tillförlitlig när det gäller säkerhets- och kvalitetsriktmärken, och du kan vara mer säker i processen att använda den. - Erfarenhet av leverantörer
Inom laserskärningsindustrin är erfarenhet en värdefull tillgång. Leverantörer med många års erfarenhet tenderar att ha djupare ackumuleringar inom teknikutveckling, produktionsprocesser och kundservice. De förstår marknadens efterfrågan bättre och kan tillhandahålla produkter av bättre kvalitet enligt kundernas olika behov. Dessutom gör deras långa erfarenhet att de kan lösa problem snabbt och effektivt och ge bättre kundservice. När du letar efter leverantörer bör du därför fokusera på deras meriter i branschen och prioritera erfarna leverantörer. - Transport- och leveransvillkor
Laserskärmaskiner är dyr utrustning och när du beställer måste du ha en grundlig förståelse för leveransvillkoren. Först och främst bör du kontrollera de leveransalternativ som tillhandahålls av leverantör av laserskärmaskin, oavsett om det är till sjöss, i luften eller på land, etc. Samtidigt bör du klargöra den beräknade tidsramen så att produktionsschemat kan rationaliseras. Fråga dessutom noga om det finns några extra kostnader som kanske inte ingick i det ursprungliga erbjudandet, t.ex. försäkringar och tullklareringsavgifter, för att undvika tvister om kostnader vid mottagandet. - Teknisk support och service efter försäljning
Att köpa en laserskärmaskin är inte en one-shot-affär, och efterföljande teknisk support och kundservice är lika viktiga. Pålitliga leverantörer kommer att ge stark teknisk support, när utrustningsfelet kan ge snabba lösningar. Samtidigt kommer de också att säkerställa en tillräcklig tillgång på reservdelar för att säkerställa att utrustningen i behov av reparation kan bytas ut i rätt tid. En omfattande garantipolicy är också ett viktigt mått på en leverantörs tillförlitlighet. När du köper bör du ta initiativ till att fråga om de tillhandahåller installationstjänster och om de kan utföra felsökning på distans, så att du effektivt kan undvika framtida användning av processen med problem med förlust.
Vill du komma i kontakt med den bästa tillverkaren av laserskärmaskiner? Klicka på knappen nu!
hur hittar jag den bästa leverantören av laserskärmaskiner för metall på e-handelsplattformen?
E-handelsplattform för oss att hitta leverantörer av laserskärmaskiner för att tillhandahålla en bekväm kanal, men samtidigt plattformen på de många leverantörerna, kvaliteten varierar, inte alla leverantörer är pålitliga. Bakom den bekväma åtkomsten ligger risken att stöta på okvalificerade leverantörer. För att säkerställa att du kan få de bästa produkterna måste du behärska några effektiva metoder.
- Använd plattformsfilter
Många e-handelsplattformar är utrustade med kraftfulla filtreringsfunktioner. De erbjuder avancerade filtreringsalternativ baserade på autentisering, användarrecensioner och transaktionshistorik. Du måste utnyttja dessa filter fullt ut, till exempel kan du ställa in filtervillkoren så att de bara visar leverantörer med CE-certifiering, användarrecensioner som uppfyller vissa standarder och en bra transaktionshistorik, vilket snabbt kan begränsa urvalet, spara tid och ansträngning och göra det möjligt för oss att hitta kvalitetsleverantörer mer exakt. - Verifiering av företagslicens
Stora plattformar som Alibaba tillhandahåller en tjänst för verifiering av leverantörer. Genom denna tjänst kan du se till att leverantörer har klarat vissa kontroller avseende deras legitimitet och pålitlighet. Genom att verifiera företagslicensen kan vi veta om leverantören är kvalificerad att bedriva laglig verksamhet, undvika att samarbeta med olaglig verksamhet eller leverantörer med dåligt rykte och skydda vår inköpssäkerhet från källan. - Begäran om produktprov
Innan du beställer i bulk är det en mycket klok praxis att be om prover. Genom att personligen utvärdera kvaliteten på provmaskinen kan du visualisera produktens prestanda, utförande och material. Du kan utföra några enkla tester på proverna, till exempel skära olika material och observera skäreffekten och precisionen etc., för att avgöra om leverantörens produkter uppfyller våra behov. - Inspektion av fabriksbesök
Pålitliga leverantörer är vanligtvis villiga att erbjuda fabriksvisningar eller virtuella videovisningar. Genom att besöka fabriken kan du se deras produktionsutrustning, produktionsprocess och kvalitetskontrollsystem med egna ögon, vilket hjälper oss att verifiera om deras annonserade produktionskapacitet är sant. Under besöket kan du också kommunicera med fabrikspersonalen för att förstå deras professionalism och arbetsattityd och ytterligare bedöma leverantörens styrka.
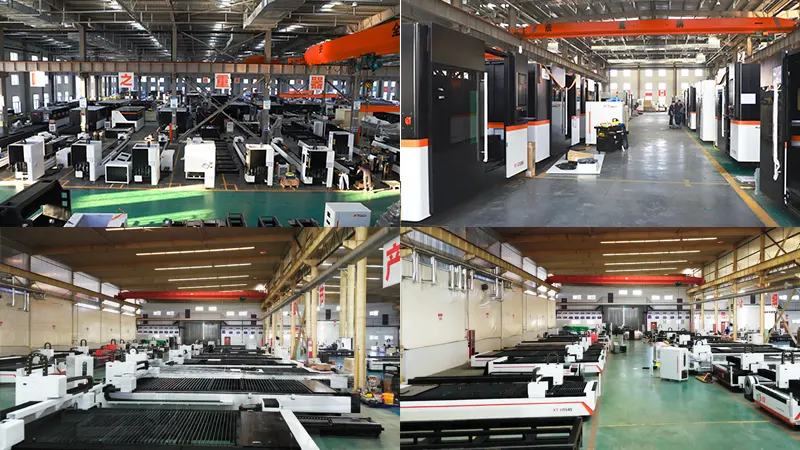
gör inte dessa 7 misstag när du väljer leverantör av laserskärningsmaskiner från webbplatsen
I processen med att leta efter leverantör av cnc fiberlaserskärmaskinVissa vanliga misstag kan få oss att fatta felaktiga beslut, vilket leder till onödiga förluster. Här är sju misstag som du absolut måste undvika.
- Ignorering av import- och exportbestämmelser
Olika länder och regioner har olika regler och skattepolitik för importerade maskiner. Till exempel kan vissa länder fastställa importkvotbegränsningar för specifika typer av laserskärmaskiner, och vissa kommer att införa högre tullar. Om du ignorerar dessa detaljer när du köper, när varorna anländer till destinationslandet, kan du möta hög skatteåterbetalning, eller till och med varorna kvarhålls, vilket utan tvekan kommer att öka vår inköpskostnad och tidskostnad. - Kontrollerar inte de dolda kostnaderna
För att locka till sig kunder anger vissa leverantörer ofta bara ett till synes lågt pris i offerten, men nämner avsiktligt inte extra kostnader som transport, hantering och importtullar. När du gör en beställning enligt detta låga pris får du bara reda på att du måste betala en hel del extra kostnader i den efterföljande transport- och tullklareringsprocessen, vilket kommer att överskrida vår budget och störa den ursprungliga upphandlingsplanen. När man kommunicerar med leverantörer måste man därför klargöra alla möjliga kostnader för att undvika att hamna i fällan med dolda kostnader. - Ignorera kompatibilitetsproblem
Laserskärmaskiner måste anslutas till en specifik strömförsörjning och kan behöva fungera tillsammans med andra befintliga maskiner i verkstaden. När du köper måste du se till att maskinen du köper är kompatibel med strömförsörjningsspänningen i det land / region där den är belägen. Till exempel är standardspänningen i vårt land 220V eller 380V, så om du köper en maskin som inte är kompatibel med denna spänning kommer den inte att kunna fungera korrekt. Samtidigt är det också nödvändigt att överväga maskinens kompatibilitet med de befintliga maskinerna i verkstaden när det gäller gränssnitt, dimensioner etc. för att undvika situationen att inte kunna matcha användningen av maskinen. - Underlåtenhet att klargöra garantivillkoren
Garantivillkor är direkt relaterade till våra rättigheter och intressen i händelse av utrustningsfel. Vissa leverantörer av laserskärningsmaskiner tillhandahåller garantitjänster, men garantin är mycket begränsad, kanske bara täcker vissa små delar, men för lasergeneratorn är styrsystemet och andra huvudkomponenter inte under garanti; eller garantiperioden är mycket kort, kan inte uppfylla den normala användningen av utrustningscykeln. Därför måste du be leverantören att tillhandahålla en detaljerad uppdelning av garantivillkoren, med angivande av garantins omfattning och varaktighet och villkoren för garantin. - Urval baserat enbart på pris
Priset är visserligen en viktig faktor att ta hänsyn till i upphandlingsprocessen, men det billigaste alternativet är inte alltid det bästa. Om vi jagar låga priser för mycket kan det leda till att vi köper produkter av dålig kvalitet, som kan gå sönder ofta under användning, vilket kräver att vi lägger mycket tid och pengar på reparationer, och deras livslängd kan också förkortas avsevärt. Du bör ta hänsyn till pris, kvalitet, teknisk support och långsiktiga kostnader för att hitta en balans mellan dessa faktorer och välja de mest kostnadseffektiva produkterna. - Hoppa över leverantörens bakgrundskontroller
Det är viktigt att undersöka leverantörernas bakgrund genom branschrapporter, online-betyg och kundfeedback. En enkel branschrapport kan avslöja information som leverantörens position, marknadsandel och rykte i branschen; online-betyg visualiserar vad andra kunder säger om dem; och kundfeedback kan ge oss en uppfattning om hur leverantören presterar i den faktiska transaktionsprocessen. Genom dessa kanaler kan du ta reda på vissa potentiella problem, till exempel om leverantör av fiberlaserskärmaskin har ofta kontraktstvister, klagomål på produktkvalitet och så vidare. - Prioriterar inte support efter försäljning
Som en slags precisionsutrustning går laserskärmaskinen oundvikligen sönder under användningen. Om leverantören inte tillhandahåller tillräckligt med kundservice kan du få en lång stilleståndstid när maskinen går sönder, vilket kommer att orsaka stora ekonomiska förluster för de produktionsorienterade företagen. När du väljer leverantörer måste du därför sätta kundservice i en viktig position och prioritera de leverantörer som kan tillhandahålla snabb och effektiv kundservice.
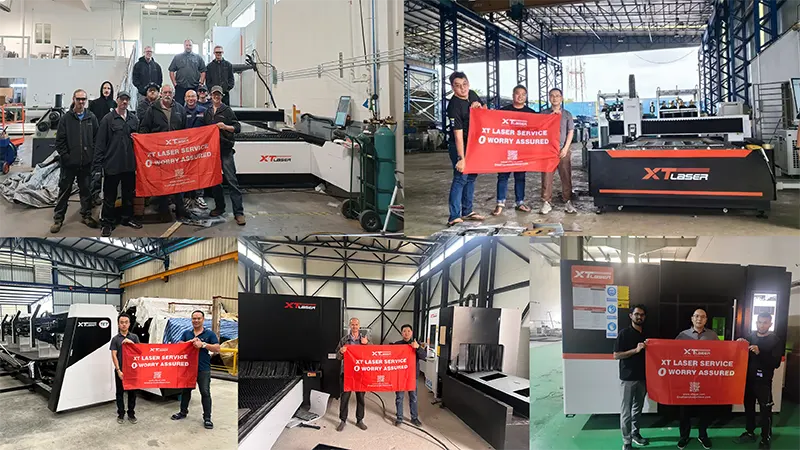
Varningstecken att undvika när du söker efter leverantörer av laserskärmaskiner online
I samband med sökandet efter leverantör av laserskärmaskin för metall online bör du alltid vara vaksam, eftersom vissa röda flaggor kan tyda på att leverantören är mindre tillförlitlig, om du ignorerar dessa signaler kan du hamna i upphandlingsrisken.
Orealistiskt låga priser
Priserna på laserskärmaskiner på marknaden har vanligtvis ett relativt rimligt intervall, och om en leverantör erbjuder ett pris som är betydligt lägre än marknadsgenomsnittet är det troligt att det är en röd flagga. Priset är för lågt kan innebära att maskinen i materialet, hantverket och andra aspekter av problemet, kvaliteten är svår att garantera; kan också ställas in av leverantören av bluffen, det första låga priset för att locka kunder att beställa, och sedan i de efterföljande länkarna genom en mängd olika sätt att fuska mer pengar. Därför, när du ser orealistiskt låga priser, måste du vara försiktig.
Bristande kommunikation
Kommunikationen med leverantörerna är en viktig del av upphandlingsprocessen. Om leverantörer är långsamma med att svara på våra förfrågningar, till exempel om du frågar om en teknisk parameter för produkten eller leveranstiden, svarar de inte på länge; eller ger vaga svar som svar, så att du inte exakt kan förstå dess betydelse, vilket allt tyder på att leverantören kanske inte kan ge bra kundsupport. I den efterföljande samarbetsprocessen, när problem uppstår, är det svårt för oss att kommunicera med dem effektivt och lösa dem.
Bristande transparens
En pålitlig leverantör av laserskärmaskin bör vara transparent, kunna tydligt tillhandahålla detaljerade produktspecifikationer, inklusive lasereffekt, skärnoggrannhet, maximal skärtjocklek och andra parametrar, så att du helt kan förstå produktens prestanda. Samtidigt, för produktcertifiering, såsom CE, ISO9001, etc., bör också kunna svara positivt och tillhandahålla relevanta styrkande handlingar. Om leverantören täcker upp i dessa områden och inte kan ge tydlig information är detta verkligen en röd flagga.
Ingen returpolicy
Under upphandlingsprocessen kan du inte helt utesluta möjligheten att få produkter som är defekta eller inte uppfyller kraven. Därför är det viktigt att se till att leverantörerna har en tydlig retur- eller utbytespolicy i händelse av defekta eller icke överensstämmande produkter. Om leverantören inte har någon returpolicy kan du ställas inför dilemmat att du inte kan returnera eller byta ut de defekta produkterna när du får dem, vilket kommer att leda till ekonomiska förluster för oss.
KONTAKTA OSS
Den ultimata checklistan för att hitta en pålitlig leverantör av laserskärmaskiner online
För att hitta tillförlitliga leverantör av fiberlaserskärmaskin online mer effektivt är det till stor hjälp att skapa en detaljerad lista, som kan spara tid och energi och göra inköpsprocessen mer organiserad.
- Plats för leverantör
Leverantörens läge påverkar transporttiden och kommunikationskostnaden. Leverantörer som ligger närmare vårt område kan vara mer praktiska när det gäller transport och kan tillhandahålla snabbare transporttjänster och förkorta leveranscykeln för varor. Dessutom kommer det att vara bekvämare att kommunicera, så att du kan göra platsbesök mer bekvämt och ha personliga utbyten och lösningar med leverantören på ett snabbare sätt när problem uppstår. - Svarstid
Leverantörernas svarstid på våra förfrågningar återspeglar i viss mån den vikt de fäster vid sina kunder och deras förmåga att ge stöd i framtiden. Om leverantörerna kan svara snabbt och korrekt när ni frågar efter produktinformation, är det också mer sannolikt att de svarar och löser problem i tid när ni stöter på problem som kräver teknisk support eller kundservice under det fortsatta samarbetet. Därför bör du i det tidiga skedet av kommunikationen med leverantörerna vara uppmärksam på att övervaka deras svarstid. - Maskinens specifikationer
Specifikationerna för laserskärmaskinen är direkt relaterade till dess förmåga att tillgodose våra produktionsbehov. Du måste fråga leverantör av laserskärmaskin för en detaljerad genomgång av maskinens funktioner, inklusive effektnivån som avgör skärningens effektivitet och tjockleksintervall, storleksspecifikationerna för att passa vår produktionsanläggning, skärhastigheten som påverkar produktionsschemat och maskinens kompatibilitet med olika material, t.ex. metall, trä, akryl etc., för att säkerställa att den kan uppfylla våra olika bearbetningsbehov. - Kontraktsinformation
Avtalet är ett viktigt dokument som skyddar våra rättigheter och intressen. Innan transaktionen slutförs är det viktigt att läsa innehållet i kontraktet noggrant och fullt ut förstå villkoren däri. I synnerhet bestämmelserna om retur, återbetalning och garantitäckning, för att klargöra under vilka omständigheter du kan returnera, återbetala, sättet och tiden för återbetalningen; garantin täcker vilka delar, garantiperioden är hur lång etc., för att undvika efterföljande tvister utan bevis att förlita sig på. - Vittnesmål från kunder
Att begära hänvisningar från tidigare kunder är ett effektivt sätt att förstå leverantörens faktiska prestanda, särskilt kunder i samma bransch som vi, vars användningsscenarier och behov liknar våra. Genom att kommunicera med dessa kunder kan du förstå stabiliteten hos leverantörens produkter i den faktiska produktionen, prestanda och kvalitet på kundservice och andra aspekter av den verkliga situationen, så att du mer exakt kan bedöma om leverantören är pålitlig.