Problemas comuns e soluções no processo de corte a laser
O corte a laser é uma tecnologia de processamento de alta precisão e alta eficiência, mas na operação real irá inevitavelmente encontrar alguns problemas comuns. A XT LASER analisará as causas destes problemas em pormenor e fornecerá as soluções correspondentes para o ajudar a melhorar eficazmente a qualidade do corte.
Arestas de corte ásperas ou rebarbas
- Análise de causas
① Potência laser insuficiente: a potência é demasiado baixa, o material não pode ser completamente derretido, resultando em arestas de corte ásperas.
② a velocidade de corte é demasiado rápida: o raio laser não permanece na superfície do material durante um período de tempo suficiente, a formação de rebarbas.
③ A distância focal não está correta: a posição de focagem do laser não é precisa, afectando a qualidade do corte.
④ Pressão de gás incorrecta: uma pressão insuficiente ou elevada do gás auxiliar conduzirá à formação de rebarbas.
⑤ Incompatibilidade das propriedades do material: os parâmetros de corte não são ajustados de acordo com o tipo e a espessura do material.
⑥ Contaminação da cabeça do laser: A sujidade ou o coque na cabeça do laser afecta a qualidade do feixe laser.
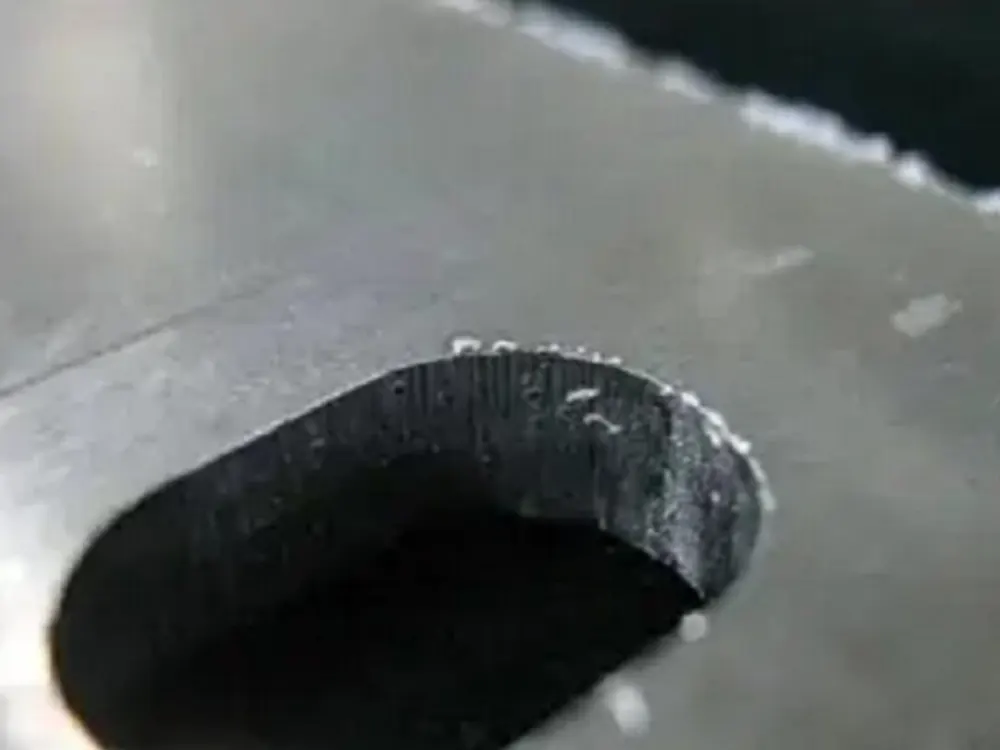
- Solução:
① Ajustar a potência do laser: Aumentar a potência do laser de forma adequada.
① Ajuste a potência do laser: Aumente a potência adequadamente para garantir que o material seja totalmente derretido.
② Otimizar a velocidade de corte: Reduzir a velocidade para que o laser tenha tempo suficiente para terminar o corte.
③ Calibrar o foco: Certifique-se de que o foco do laser é preciso e que a posição do foco deve estar na superfície do material ou ligeiramente abaixo dela.
④ Ajustar a pressão do gás: Ajuste a pressão do gás auxiliar de acordo com as caraterísticas do material e certifique-se de que a taxa de fluxo é estável.
⑤ Escolha os parâmetros adequados: compreenda as caraterísticas do material e defina a potência e a velocidade de corte de forma razoável.
⑥ Limpar a cabeça do laser: Limpe a cabeça do laser regularmente para manter o equipamento em boas condições.
A secção de corte é demasiado larga ou ocorre um fenómeno de fusão
- Análise de causas
① A potência do laser é muito alta: a configuração de potência é muito alta, resultando em derretimento excessivo do material.
② a velocidade de corte é demasiado lenta: demasiado lenta para fazer com que o laser permaneça demasiado tempo, aumentando a zona afetada pelo calor.
③ Imprecisão da distância focal: localização incorrecta do ponto focal que conduz a um aumento do diâmetro do feixe laser.
④ fluxo de gás auxiliar insuficiente: o fluxo de gás insuficiente não pode soprar o metal fundido, exacerbando o fenómeno de fusão.
⑤ As caraterísticas do material não são adequadas: certos materiais ou materiais com maior espessura têm maior probabilidade de derreter.
⑥ Má qualidade do feixe de laser: A má uniformidade do feixe de laser ou o ângulo de divergência afectarão o efeito de corte.
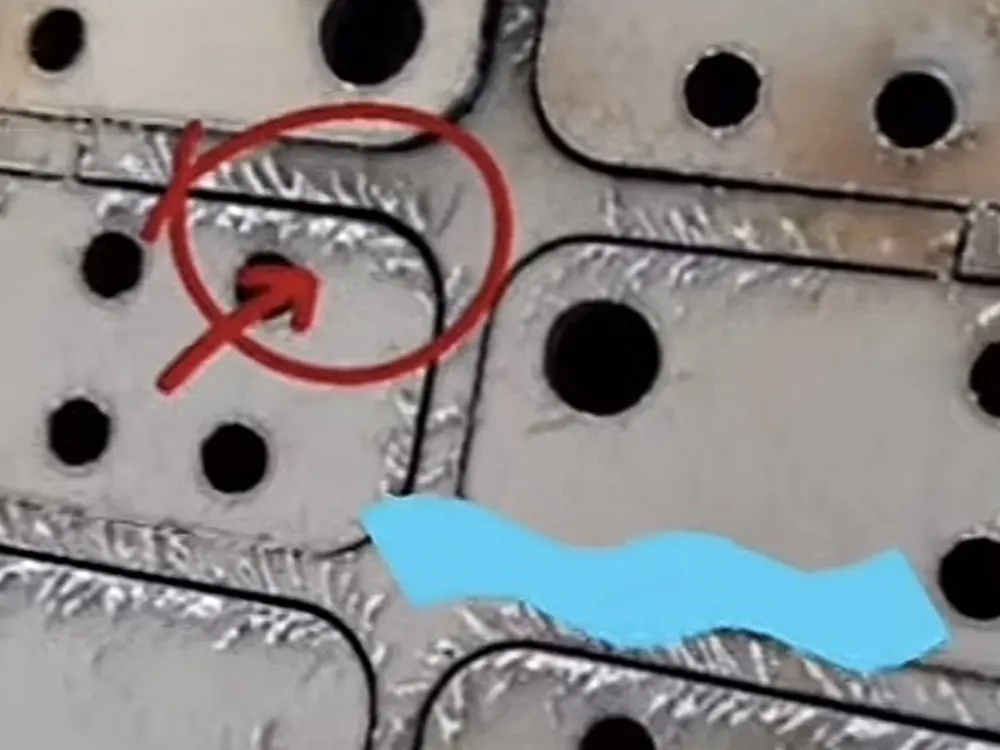
- Solução
① Reduzir a potência do laser: de acordo com as caraterísticas do material da redução adequada da potência do laser.
② Aumentar a velocidade de corte: Ajustar a velocidade para evitar problemas de fusão causados por uma velocidade demasiado lenta.
Calibrar a distância focal: Verificar se a posição de focagem do laser está correta.
④ Aumente o caudal de gás auxiliar: Certifique-se de que o fluxo de gás é suficiente para soprar o metal fundido de forma eficaz.
⑤ Selecione o material e os parâmetros adequados: Antes de cortar, ajuste os parâmetros de forma razoável para se adequar às caraterísticas do material.
⑥ Melhorar a qualidade do feixe laser: Faça a manutenção do equipamento laser regularmente para garantir a qualidade do feixe de laser.
A superfície de corte não é plana e tem ondulações
- Análise de causas
① Flutuação da potência do laser: a saída instável do laser leva a uma distribuição desigual da energia.
② velocidade de corte não é uniforme: mudanças de velocidade afetam o feixe de laser na superfície do tempo do material.
③ Imprecisão da distância focal: localização incorrecta do ponto focal, diminuição da qualidade de corte.
④ deformação ou irregularidade do material: a deformação do material ou a irregularidade da superfície afectam o efeito de corte.
⑤ Vibração da cabeça do laser: a falta de estabilidade mecânica do equipamento pode produzir vibração.
⑥ Fluxo de gás auxiliar instável: o fluxo de gás instável afecta o efeito de sopro do metal fundido.

- Solução
Estabilizar a potência do laser: Defina uma potência máxima e mínima razoável para garantir uma saída de laser estável.
② Otimizar a velocidade de corte: Manter a velocidade consistente e evitar a flutuação da velocidade durante o corte.
③ Calibrar o foco: ajustar a posição do foco do laser regularmente para garantir a precisão do corte.
④ Verificar a planicidade do material: endireitar o material antes de cortar para evitar afetar a qualidade do corte devido a deformações.
⑤ Melhorar a estabilidade da cabeça do laser: Verifique e aperte as peças mecânicas da cabeça do laser para reduzir a vibração.
⑥ Controlo do fluxo de gás: Assegurar que o fluxo de gás auxiliar é estável para melhorar a qualidade da superfície de corte.
Faíscas anormais durante o corte
- Análise de causas
① A potência do laser é demasiado elevada: uma definição de potência do laser demasiado elevada pode levar a uma fusão excessiva do material, gerando um grande número de faíscas.
② a velocidade de corte é demasiado lenta: uma velocidade de corte demasiado lenta fará com que o laser permaneça no material durante demasiado tempo, aumentando a geração de faíscas.
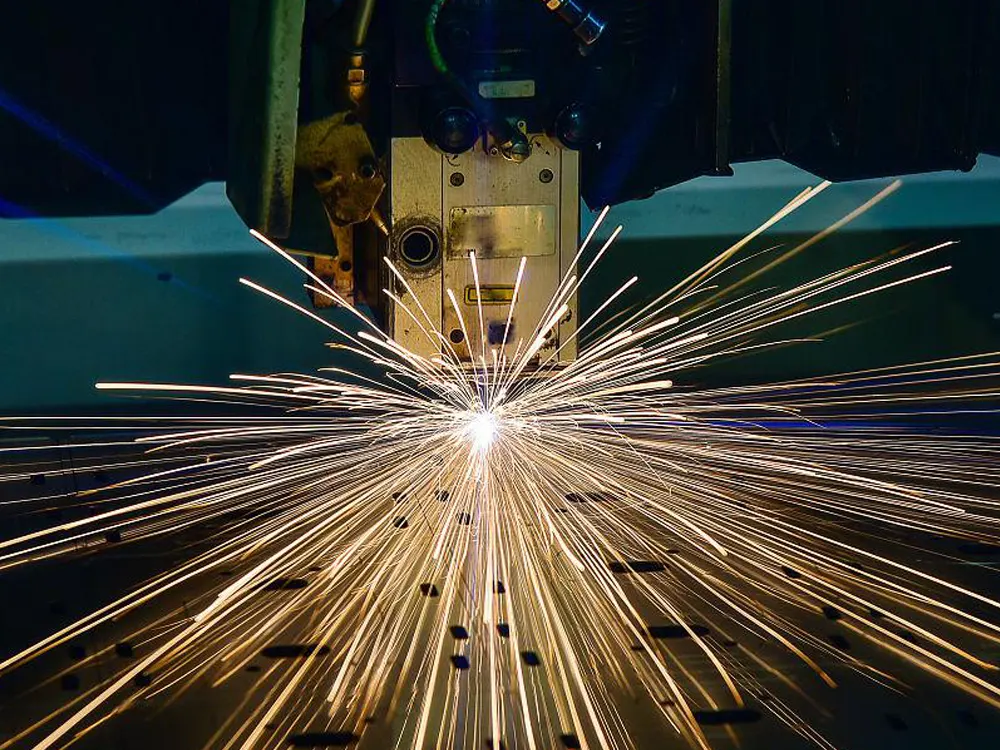
- Solução
① Ajustar a potência do laser: Reduzir a potência do laser adequadamente de acordo com a espessura e o tipo de material para reduzir a geração de faíscas.
② Otimizar a velocidade de corte: Aumente a velocidade de corte para garantir que o laser actua no material durante o tempo adequado para evitar faíscas causadas por uma velocidade demasiado lenta.
Os problemas de qualidade durante o corte a laser têm normalmente origem nas definições dos parâmetros, nas caraterísticas do material ou numa manutenção inadequada do equipamento. Ajustando a potência, a velocidade, a distância focal e optimizando o fluxo de gás auxiliar, etc., a qualidade do corte pode ser efetivamente melhorada.