Typowe problemy i rozwiązania w procesie cięcia laserowego
Cięcie laserowe jest wysoce precyzyjną i wysokowydajną technologią przetwarzania, ale w rzeczywistej pracy nieuchronnie napotka pewne typowe problemy. XT LASER szczegółowo przeanalizuje przyczyny tych problemów i zapewni odpowiednie rozwiązania, które pomogą skutecznie poprawić jakość cięcia.
Szorstkie krawędzie tnące lub zadziory
- Analiza przyczyn
① Niewystarczająca moc lasera: moc jest zbyt niska, materiał nie może zostać całkowicie stopiony, co skutkuje szorstkimi krawędziami tnącymi.
② prędkość cięcia jest zbyt duża: wiązka lasera nie pozostaje na powierzchni materiału przez wystarczający okres czasu, co powoduje powstawanie zadziory.
③ Ogniskowa nie jest prawidłowa: pozycja ogniskowania lasera nie jest dokładna, co wpływa na jakość cięcia.
④ Niewłaściwe ciśnienie gazu: niewystarczające lub wysokie ciśnienie gazu pomocniczego prowadzi do powstawania zadziorów.
⑤ Niedopasowanie właściwości materiału: parametry cięcia nie są dostosowane do rodzaju i grubości materiału.
⑥ Zanieczyszczenie głowicy lasera: Brud lub koks na głowicy lasera wpływa na jakość wiązki laserowej.
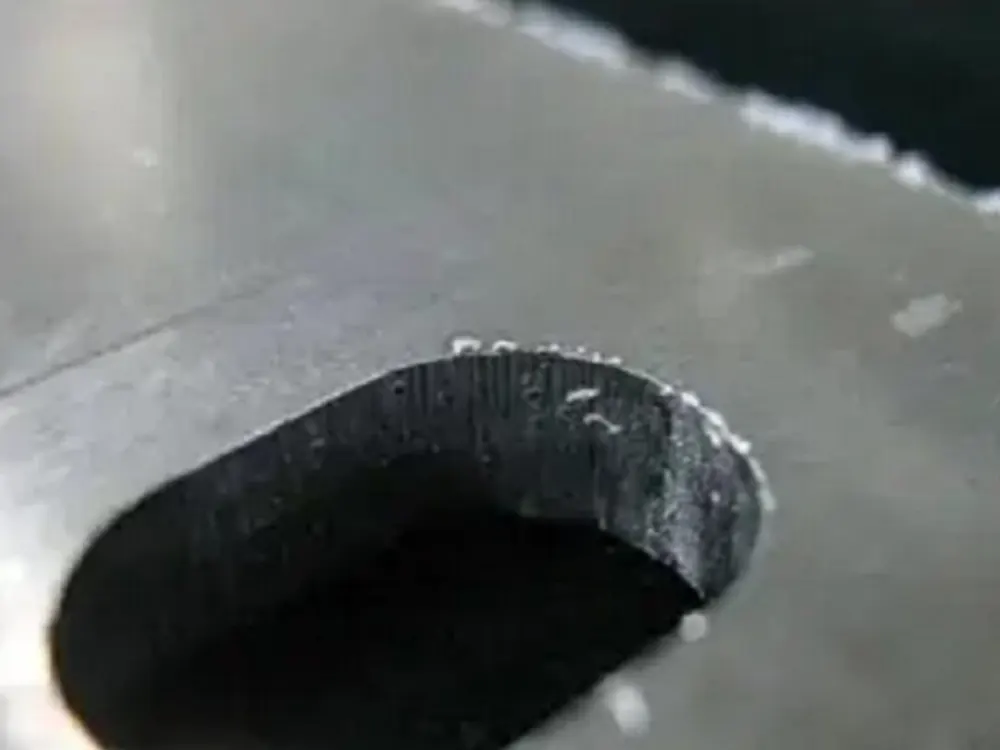
- Rozwiązanie:
① Regulacja mocy lasera: Odpowiednio zwiększ moc lasera.
① Dostosuj moc lasera: Odpowiednio zwiększ moc, aby zapewnić całkowite stopienie materiału.
② Optymalizacja prędkości cięcia: Zmniejsz prędkość, aby laser miał wystarczająco dużo czasu na zakończenie cięcia.
③ Skalibrować ostrość: Upewnij się, że ostrość lasera jest dokładna, a pozycja ostrości powinna znajdować się na powierzchni materiału lub nieco poniżej niej.
④ Wyregulować ciśnienie gazu: Wyreguluj ciśnienie gazu pomocniczego zgodnie z charakterystyką materiału i upewnij się, że natężenie przepływu jest stabilne.
⑤ Wybór odpowiednich parametrów: zrozumienie charakterystyki materiału i rozsądne ustawienie mocy i prędkości cięcia.
⑥ Czyszczenie głowicy lasera: Należy regularnie czyścić głowicę lasera, aby utrzymać urządzenie w dobrym stanie.
Sekcja cięcia jest zbyt szeroka lub występuje zjawisko topnienia
- Analiza przyczyn
① Moc lasera jest zbyt wysoka: ustawienie mocy jest zbyt wysokie, co powoduje nadmierne stopienie materiału.
② prędkość cięcia jest zbyt niska: zbyt niska prędkość powoduje, że laser pozostaje zbyt długo, zwiększając strefę wpływu ciepła.
③ Niedokładność ogniskowej: niewłaściwa lokalizacja punktu ogniskowego prowadząca do zwiększenia średnicy wiązki laserowej.
④ niewystarczający przepływ gazu pomocniczego: niewystarczający przepływ gazu nie może zdmuchnąć stopionego metalu, co pogarsza zjawisko topienia.
⑤ Charakterystyka materiału nie jest odpowiednia: niektóre materiały lub materiały o większej grubości są bardziej podatne na stopienie.
⑥ Słaba jakość wiązki laserowej: Słaba jednorodność wiązki laserowej lub kąt rozbieżności wpływają na efekt cięcia.
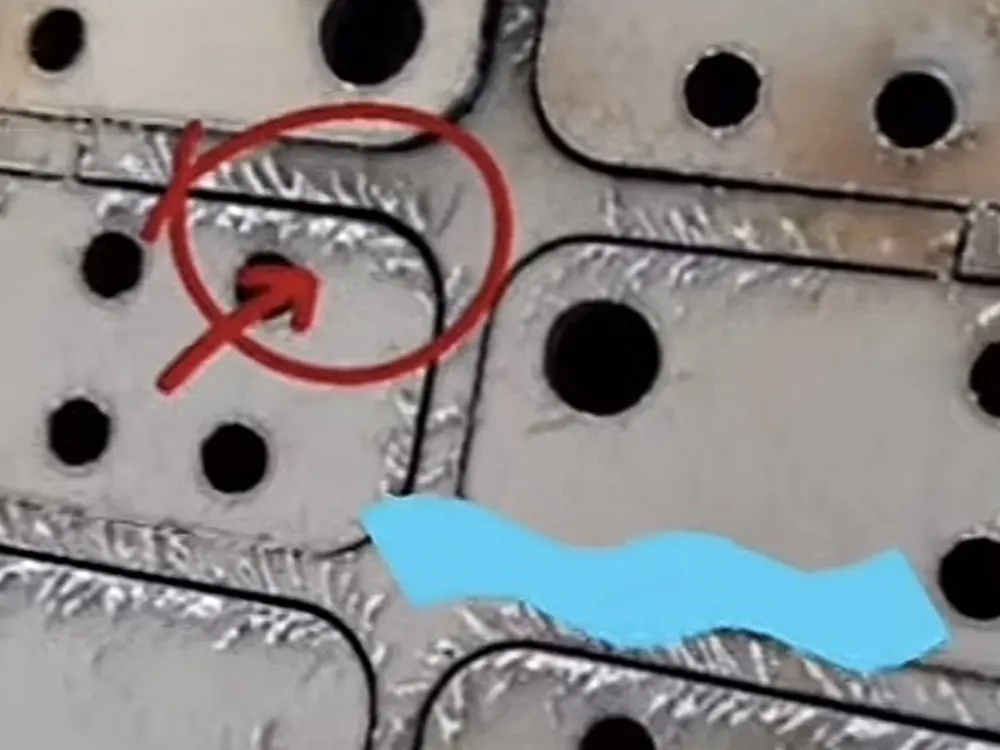
- Rozwiązanie
① Zmniejszenie mocy lasera: zgodnie z charakterystyką materiału odpowiednie zmniejszenie mocy lasera.
② Zwiększenie prędkości cięcia: Dostosuj prędkość, aby uniknąć problemów z topieniem spowodowanych zbyt niską prędkością.
Skalibruj ogniskową: Upewnij się, że pozycja ogniskowania lasera jest prawidłowa.
④ Zwiększyć przepływ gazu pomocniczego: Upewnić się, że przepływ gazu jest wystarczający do skutecznego wydmuchiwania stopionego metalu.
⑤ Wybrać odpowiedni materiał i parametry: Przed rozpoczęciem cięcia należy odpowiednio dostosować parametry do charakterystyki materiału.
⑥ Poprawa jakości wiązki laserowej: Regularna konserwacja sprzętu laserowego zapewnia jakość wiązki laserowej.
Powierzchnia tnąca nie jest płaska i występują na niej zmarszczki
- Analiza przyczyn
① Wahania mocy lasera: niestabilna moc wyjściowa lasera prowadzi do nierównomiernego rozkładu energii.
② prędkość cięcia nie jest jednolita: zmiany prędkości wpływają na wiązkę lasera na powierzchni materiału w czasie.
③ Niedokładność ogniskowej: niewłaściwa lokalizacja punktu ogniskowego, spadek jakości cięcia.
④ deformacja lub nierówności materiału: wypaczenie materiału lub nierówności powierzchni wpływają na efekt cięcia.
⑤ Wibracje głowicy lasera: brak stabilności mechanicznej sprzętu może powodować wibracje.
⑥ niestabilny przepływ gazu pomocniczego: niestabilny przepływ gazu wpływa na efekt wydmuchiwania stopionego metalu.

- Rozwiązanie
① Stabilizacja mocy lasera: Ustaw rozsądną moc maksymalną i minimalną, aby zapewnić stabilną moc lasera.
② Optymalizacja prędkości cięcia: Utrzymuj stałą prędkość i unikaj wahań prędkości podczas cięcia.
③ Kalibracja ogniskowania: regularnie reguluj położenie ogniskowania lasera, aby zapewnić dokładność cięcia.
④ Sprawdź płaskość materiału: wyprostuj materiał przed cięciem, aby uniknąć wpływu wypaczenia na jakość cięcia.
⑤ Zwiększenie stabilności głowicy lasera: Sprawdź i dokręć mechaniczne części głowicy lasera, aby zmniejszyć wibracje.
⑥ Kontrola przepływu gazu: Zapewnienie stabilnego przepływu gazu pomocniczego w celu poprawy jakości powierzchni cięcia.
Nieprawidłowe iskry podczas cięcia
- Analiza przyczyn
① Zbyt wysoka moc lasera: zbyt wysokie ustawienie mocy lasera może prowadzić do nadmiernego stopienia materiału, generując dużą liczbę iskier.
② zbyt niska prędkość cięcia: zbyt niska prędkość cięcia powoduje, że laser zbyt długo pozostaje na materiale, co zwiększa wytwarzanie iskier.
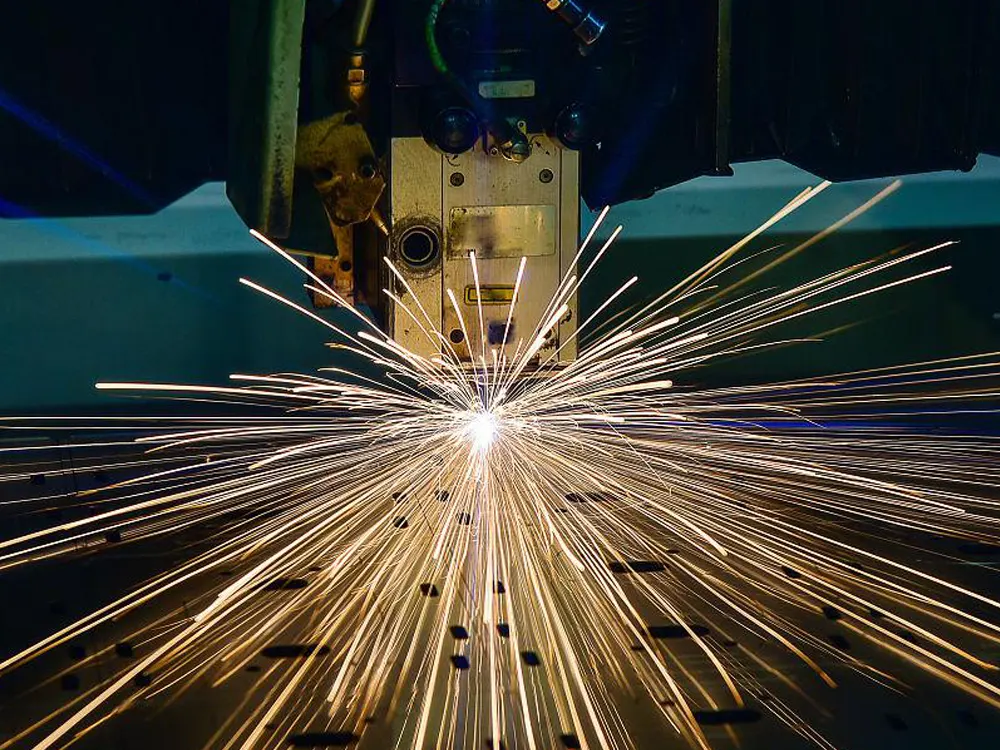
- Rozwiązanie
① Wyregulować moc lasera: Zmniejsz moc lasera odpowiednio do grubości i rodzaju materiału, aby zmniejszyć wytwarzanie iskier.
② Zoptymalizuj prędkość cięcia: Zwiększ prędkość cięcia, aby laser działał na materiał przez odpowiedni czas i aby uniknąć iskrzenia spowodowanego zbyt wolną pracą.
Problemy z jakością podczas cięcia laserowego zazwyczaj wynikają z ustawień parametrów, charakterystyki materiału lub nieodpowiedniej konserwacji sprzętu. Dostosowując moc, prędkość, ogniskową i optymalizując przepływ gazu pomocniczego itp. można skutecznie poprawić jakość cięcia.