레이저 커팅 공정의 일반적인 문제와 해결 방법
레이저 절단은 고정밀, 고효율 가공 기술이지만 실제 작업에서는 필연적으로 몇 가지 일반적인 문제에 직면하게 됩니다. XT LASER는 이러한 문제의 원인을 자세히 분석하고 해당 솔루션을 제공하여 절단 품질을 효과적으로 향상시킬 수 있도록 도와드립니다.
거친 절단면 또는 버
- 원인 분석
레이저 출력 부족: 출력이 너무 낮아서 재료를 완전히 녹일 수 없어 절단면이 거칠어집니다.
절단 속도가 너무 빠름 : 레이저 빔이 재료 표면에 충분한 시간 동안 머물러 있지 않습니다. burrs.
초점 거리가 정확하지 않음: 레이저 초점 위치가 정확하지 않아 절단 품질에 영향을 미칩니다.
부적절한 가스 압력: 보조 가스의 압력이 충분하지 않거나 높으면 버가 형성될 수 있습니다.
재료 특성의 불일치: 재료의 종류와 두께에 따라 절단 매개변수가 조정되지 않습니다.
레이저 헤드 오염: 레이저 헤드의 먼지나 코크스는 레이저 빔의 품질에 영향을 미칩니다.
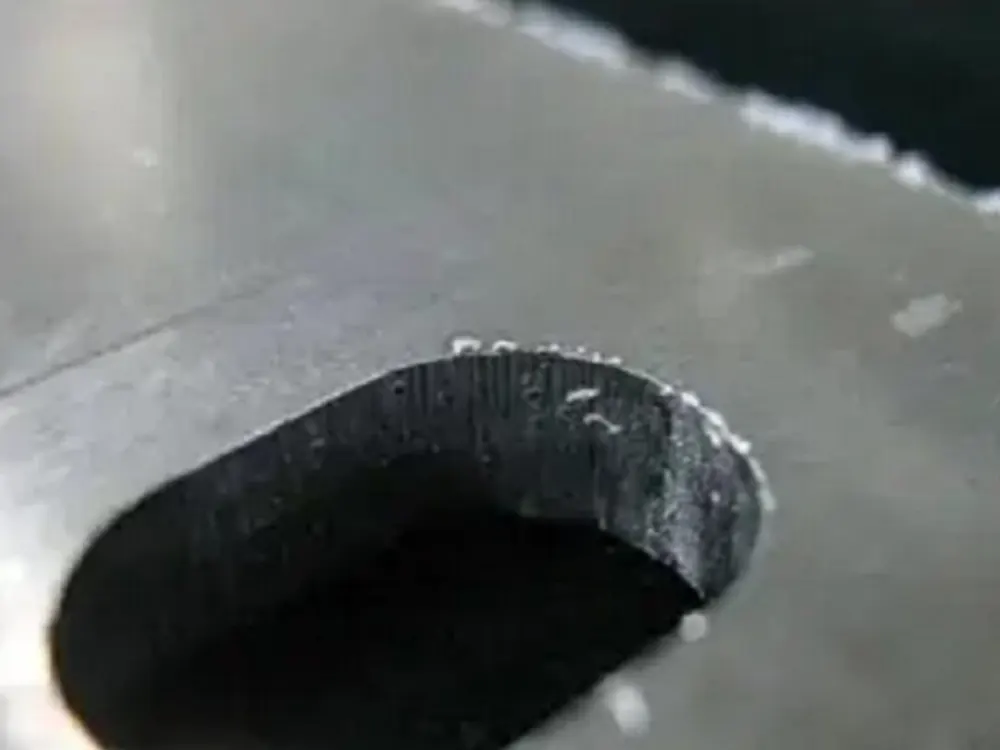
- 솔루션:
레이저 출력 조정: 레이저 출력을 적절히 높입니다.
레이저 출력 조절: 재료가 완전히 녹을 수 있도록 출력을 적절히 높입니다.
절단 속도를 최적화합니다: 레이저가 절단을 완료할 수 있는 충분한 시간을 갖도록 속도를 줄입니다.
초점을 보정합니다: 레이저 초점이 정확한지 확인하고 초점 위치가 재료 표면 위 또는 약간 아래에 있어야 합니다.
가스 압력을 조절합니다: 재료 특성에 따라 보조 가스 압력을 조정하고 유량이 안정적인지 확인합니다.
적합한 매개변수 선택: 재료 특성을 이해하고 절단력과 속도를 합리적으로 설정합니다.
레이저 헤드를 청소합니다: 레이저 헤드를 정기적으로 청소하여 장비를 양호한 상태로 유지하세요.
절단 단면이 너무 넓거나 녹는 현상이 발생합니다.
- 원인 분석
레이저 출력이 너무 높음: 출력 설정이 너무 높아서 재료가 과도하게 녹습니다.
절단 속도가 너무 느림: 레이저가 너무 느려서 레이저가 너무 오래 머물러 열 영향 영역이 증가합니다.
초점 거리 부정확성: 초점의 부적절한 위치로 인해 레이저 빔의 직경이 증가하는 경우.
불충분 한 보조 가스 흐름 : 불충분 한 가스 흐름은 용융 금속을 날려 버릴 수 없어 용융 현상을 악화시킵니다.
재료 특성이 적합하지 않은 경우: 특정 재료 또는 두께가 두꺼운 재료는 녹을 가능성이 더 높습니다.
레이저 빔 품질 불량: 레이저 빔의 균일성 또는 발산 각도가 좋지 않으면 절단 효과에 영향을 미칩니다.
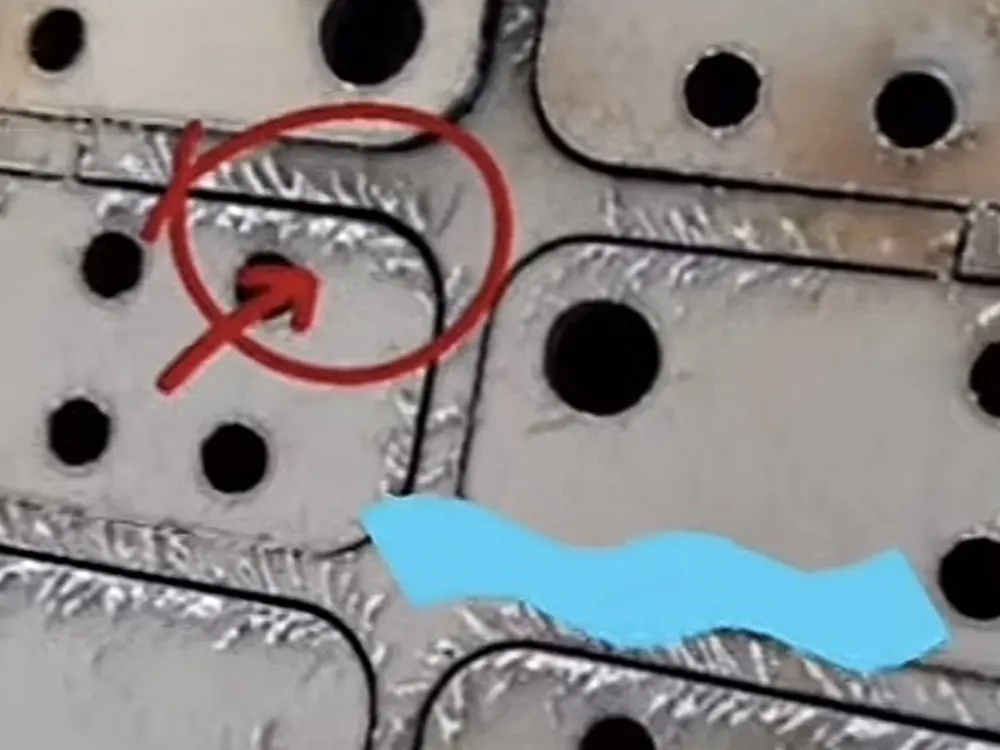
- 솔루션
레이저 출력 감소: 레이저 출력의 적절한 감소의 재료 특성에 따라.
절단 속도를 높입니다: 너무 느려서 녹는 문제를 방지하기 위해 속도를 조절합니다.
초점 거리를 보정합니다: 레이저 초점 위치가 올바른지 확인합니다.
보조 가스 유량을 늘립니다: 용융 금속을 효과적으로 날려버릴 수 있을 만큼 가스 흐름이 충분한지 확인합니다.
적절한 소재와 파라미터를 선택합니다: 절단하기 전에 재료 특성에 맞게 파라미터를 합리적으로 조정합니다.
레이저 빔 품질을 개선합니다: 레이저 빔 품질을 보장하기 위해 레이저 장비를 정기적으로 유지 관리합니다.
절단면이 평평하지 않고 잔물결이 있습니다.
- 원인 분석
레이저 출력 변동: 레이저 출력이 불안정하면 에너지 분포가 고르지 않게 됩니다.
절단 속도가 균일하지 않음: 속도 변화는 재료 표면의 레이저 빔에 영향을 미칩니다.
초점 거리 부정확성: 초점의 부적절한 위치, 커팅 품질 저하.
재료 변형 또는 요철: 재료 뒤틀림이나 표면 요철이 절단 효과에 영향을 미칩니다.
레이저 헤드 진동: 장비의 기계적 안정성이 부족하면 진동이 발생할 수 있습니다.
불안정한 보조 가스 흐름: 불안정한 가스 흐름은 용융 금속의 블로잉 효과에 영향을 미칩니다.

- 솔루션
레이저 출력 안정화: 안정적인 레이저 출력을 보장하기 위해 합리적인 최대 및 최소 출력을 설정합니다.
절단 속도 최적화: 절단 중 속도 변동을 피하고 속도를 일정하게 유지하세요.
초점 보정: 절단 정확도를 보장하기 위해 레이저 초점 위치를 정기적으로 조정합니다.
재료 평탄도 확인: 뒤틀림으로 인한 절단 품질에 영향을 미치지 않도록 절단하기 전에 재료를 곧게 펴세요.
레이저 헤드의 안정성을 강화합니다: 레이저 헤드의 기계 부품을 점검하고 조여 진동을 줄입니다.
가스 흐름을 제어합니다: 절단 표면의 품질을 향상시키기 위해 보조 가스 흐름이 안정적인지 확인합니다.
절단 중 비정상적인 스파크 발생
- 원인 분석
레이저 출력이 너무 높음: 레이저 출력을 너무 높게 설정하면 재료가 과도하게 용융되어 많은 스파크가 발생할 수 있습니다.
절단 속도가 너무 느림: 절단 속도가 너무 느리면 레이저가 재료에 너무 오래 머무르게 되어 스파크 발생이 증가합니다.
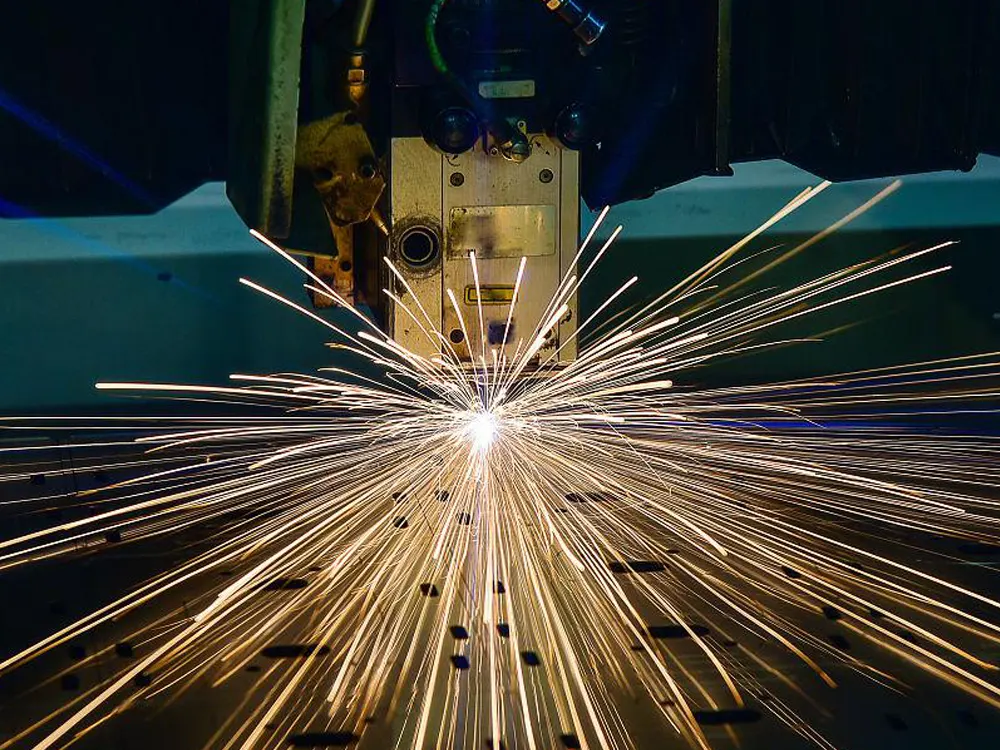
- 솔루션
레이저 출력을 조절합니다: 재료의 두께와 종류에 따라 레이저 출력을 적절히 줄여 스파크 발생을 줄이세요.
절단 속도 최적화: 절단 속도를 높여 레이저가 재료에 적절한 시간 동안 작용하도록 하여 너무 느려서 스파크가 발생하지 않도록 합니다.
레이저 절단 중 품질 문제는 일반적으로 매개변수 설정, 재료 특성 또는 부적절한 장비 유지보수에서 비롯됩니다. 출력, 속도, 초점 거리 등을 조정하고 보조 가스의 흐름을 최적화하면 절단 품질을 효과적으로 개선할 수 있습니다.