壮大な橋梁から複雑な電子部品に至るまで、溶接技術はどこにでもある。技術の絶え間ない進歩に伴い、溶接方法も常に革新されている。レーザー溶接は、新しい高エネルギー・ビーム溶接技術として、その高精度、高効率、低変形性により、様々な分野で徐々に台頭し、従来の溶接方法に大きな課題を投げかけています。
この記事では、レーザー溶接と従来の溶接方法の比較について、動作原理、長所と短所、適用範囲などさまざまな観点から詳しく説明します。これにより、レーザー溶接と他の溶接方法の利点と限界をより包括的に理解することができ、各業界に適した溶接方法を選択する際の参考となります。
レーザー溶接の仕組み
レーザー溶接は、レーザーを熱源として材料を加熱し、溶融させて接合する。レーザーは単色性と指向性に優れているため、非常に微細なスポットに容易に集光でき、スポット内のエネルギー密度も極めて高い。したがって、レーザー溶接の主な特徴は、溶接シームの深さと幅の比が大きいことである。
レーザー溶接は大気中で行うことができ、加工要件に応じてシールド・ガスを使用することもある。レーザーは高融点材料の溶接が可能で、場合によっては異種材料の溶接も実現できる。
産業用レーザー、制御技術、および工作機械の発展に伴い、ファイバーレーザー溶接機は、より小型でコンパクト、効率的、耐久性、および信頼性の高いものへと進化しています。ファイバー・レーザー溶接機は、操作の柔軟性と自動化レベルを高めるために、コンピューター、回転可能なレンズ、マルチチャンネル・ビーム分割、およびファイバー伝送を装備しています。
レーザー溶接の利点
- レーザー照射時間が短い 超高速 溶接工程
これは生産性の向上に役立つだけでなく、溶接材料が酸化しにくくなる。熱影響部が小さいため、熱に非常に敏感なトランジスター部品の溶接に適している。レーザー溶接ではスラグが発生せず、ワークから酸化皮膜を除去する必要もない。ガラス越しの溶接も可能で、以下のような特長がある。 特に 小型精密機器の溶接に適している。
- 異種材料の溶接
レーザーは同種の金属材料だけでなく、異種の金属材料、さらには金属と非金属材料の溶接も可能である。例えば、集積回路のベースとしてセラミックを使用することは困難である。 と セラミックは融点が高く、圧力を加えるのは好ましくないため、他の溶接法では不可能である。しかし、レーザー溶接はこれを比較的容易にする。もちろん、レーザー溶接はすべての異種材料を溶接できるわけではない。
- 高い 自動化の度合い
レーザー溶接は、自動化とインテリジェント制御が容易です。CNCシステムとロボット技術により、高精度で高効率な溶接工程を実現し、手作業を減らし、生産性を向上させ、人件費を削減することができます。
一般的な溶接方法とは?それぞれの違いは何ですか?
従来の溶接方法の動作原理と特性を理解することは、レーザー溶接と他の溶接方法の違いを理解することに役立ち、その結果、お客様のニーズに適した溶接方法が明確になります。
アーク溶接
アーク溶接は、電極と金属ワークの間に発生する激しい電気アークを熱源として利用する。アークの高温は、電極と金属加工物を局部的に溶かす。電極内の溶加材も溶けて溶融池に入る。 溶けたプールが冷えて固まった後、 それが 電極と被加工物をつなぐ溶接継ぎ目。
アーク溶接には、SMAW(シールド金属アーク溶接)、MIG溶接(金属不活性ガス溶接)、TIG溶接(タングステン不活性ガス溶接)、プラズマ・アーク溶接、サブマージアーク溶接など、多くの種類がある。
レーザー溶接とアーク溶接の比較
- レーザー溶接は高エネルギー密度のレーザービームを熱源とし、アーク溶接は電極とワークの間に発生する電気アークを利用する。レーザー・ビームのエネルギーが集中するため、入熱量が低く、熱影響部が狭く、溶接変形が少ない。 溶接 や薄板溶接に適している。対照的に、アーク溶接は入熱が大きく、熱影響部が自然に広くなり、溶接変形が大きくなるため、大型の構造部品の溶接に適している。
- レーザー溶接は、より高速である。 溶接 アーク溶接よりも速度が速く、精度と溶接品質が高い。レーザー溶接は、溶加材を必要としない非接触の溶接プロセスであり、溶接プロセスは無煙で自動化が容易である。アーク溶接 必要 溶加材は、溶接プロセスでヒュームとアーク放射を発生させ、その結果、次のような問題を引き起こす。 いくつか 環境汚染、自動化の度合いが低い。
- レーザー溶接装置のコストは比較的高く、特定の分野での適用が制限されている。アーク溶接装置は低コストで操作が簡単なため、溶接品質や精度の要求が高くなく、構造が単純な場合に適している。
ろう付け
ろう付けは、母材よりも融点の低い金属フィラーを使用してワークを接合するプロセスである。ワークピースと金属フィラーを、金属フィラーの融点以上母材の融点未満の温度に加熱する。溶融した金属フィラーは毛細管現象によって接合隙間に流入し、母材表面を濡らし、原子拡散を受ける。冷却して凝固すると、ワークピースをつなぐろう付け接合部が形成される。
レーザー溶接とろう付けの比較
- レーザー溶接は、高エネルギー密度のレーザービームを利用して被加工物を局部的に溶かし、溶融池を形成して冷却時に凝固して接合部を形成する。一方、ろう付けは、母材よりも融点の低い金属フィラーを使用する。溶融するまで加熱され、毛細管現象によって接合部のギャップを埋め、冷却時に凝固して接合部を形成する。そのため、レーザー溶接は母材を直接溶融・融合させることになり、母材の強度に近い高い接合強度が得られる。一方、ろう付けの接合強度は比較的低く、ろう材の強度に制限される。
- レーザー溶接は、さまざまな金属や一部の非金属、特に高融点金属や耐火性金属に適している。ろう付けは ふさわしい にとって 様々な 金属材料、特に異種金属、薄板、精密部品の接合。
- レーザー溶接は、自動車、航空宇宙、電子機器、医療機器など、高い溶接品質と精度が求められる分野で広く使用されている。ろう付けは 広く 冷凍、空調、計装、宝飾、その他、接合強度はそれほど要求されないが、良好なシール性と電気・熱伝導性が必要な分野で使用される。
電子ビーム溶接 (EBW)
電子ビーム溶接は高真空環境で行われる。電子銃から電子ビームが放出される、 それは 高電圧によって加速され、電磁レンズによって集束される。ビームは被加工物の表面に照射され、運動エネルギーを熱エネルギーに変換し、被加工物を加工します。 への ローカルメルト そして溶接を達成する.
レーザー溶接とEBWの比較
- レーザー溶接は、エネルギー源としてレーザー・ビームを使用し、大気中またはシールド・ガス環境で行うことができる。 EBWは高真空環境で加速された電子ビームを利用する そして は真空チャンバー内で行わなければならない。 このため、レーザー溶接は操作の柔軟性において有利であるが、EBWは設備と操作環境に対する要求が高い。
- EBWのエネルギー密度は、一般にレーザー溶接よりも高く、より深い溶け込みと狭い溶接継ぎ目を可能にするため、特に厚板溶接や高融点材料の接合に適している。レーザー溶接はエネルギー密度が比較的低いが、ビームの制御と集束が容易なため、精密溶接や複雑な形状の部品の接合に適している。
- エネルギー密度が高いため、EBWの熱影響部はレーザー溶接よりも小さく、溶接変形や残留応力を低減できる。これは、熱に敏感な材料や精密部品の溶接に特に重要である。
- EBWは、チタンのような高融点、高強度、酸化しやすい材料の溶接に適している。 合金 および高温合金を含む。レーザー溶接は、さまざまな金属や一部の非金属材料を含む、より幅広い用途がある。
- EBW装置は高価で、真空システムなどの補助装置を必要とするが、レーザー溶接装置は比較的安価である。そのため、EBWは主に航空宇宙、原子力産業、精密機器など、溶接品質要求が極めて高い分野で使用されている。レーザー溶接は、自動車、電子機器、医療、その他の産業など、より幅広い分野で応用されている。
マイクロ溶接
マイクロウェルディングは、高エネルギー密度の熱源を利用し、ミクロのスケールで接続を実現する精密接合技術である。その作業原理は通常、熱源(レーザービーム、電気アーク、電子ビームなど)をマイクロメートルまたはサブミリメートルのスポットサイズに集中させ、ワークピースの局所領域を急速に溶融させて材料の接合を実現する。
レーザー溶接とマイクロ溶接
- マイクロ溶接は主に、マイクロメートルまたはサブマイクロメートルの範囲の寸法を伴う、小型部品や微細構造の接合に使用される。レーザー溶接は応用範囲が広く、極小部品から大型構造物までの溶接に使用できる。
- マイクロ溶接は通常、溶接速度が速く、大量生産に適している。レーザー溶接も高速だが、小型部品の溶接にはマイクロ溶接の方が効率的かもしれない。
- マイクロ溶接もレーザー溶接も、さまざまな金属や一部の非金属材料に適している。しかし、マイクロ溶接は熱影響部が小さいため、一部の特殊材料(生体材料や電子部品など)の接合には有利で、材料の特性への損傷を避けることができる。
抵抗溶接
抵抗溶接は、溶接によって発生する抵抗熱を利用する。 現行の 熱源として、ワークの接触面および隣接する領域を介して。加圧下でワークピースを局部的に溶融させ、接合を実現する。抵抗溶接の主な種類には、スポット溶接、シーム溶接、プロジェクション溶接、突き合わせ溶接、フラッシュ溶接、高周波溶接などがある。
レーザー溶接と抵抗溶接
- レーザー溶接は、高エネルギー密度のレーザービームを熱源とし、非接触で溶接を行う。これに対し、抵抗溶接は、溶接金属から発生する抵抗熱を利用する。 現行の を通るため、ワークと直接接触する必要がある。したがって、レーザー溶接は複雑な形状のワークや手の届きにくいワークに適しており、抵抗溶接は重ね継手や突合せ継手のような単純な形状のワークに適している。
- レーザー溶接は入熱を正確に制御できるため、熱影響部が小さく、溶接変形が最小限に抑えられる。このため、精密溶接や熱に敏感な材料の溶接に適している。一方、抵抗溶接は入熱量が比較的大きく、熱影響部が広く、溶接変形が大きいため、溶接変形があまり気にならない場合に適している。
- レーザー溶接は溶接速度が速く、効率が高いため、大量生産に適している。抵抗溶接は溶接速度が比較的遅く、量産に適している。 ふさわしい 小・中ロット生産向け。レーザー溶接装置は高価で、専門のオペレーターを必要とするが、抵抗溶接装置はコストが安く、操作が簡単で、容易に自動化できる。
- レーザー溶接は、さまざまな金属や一部の非金属材料の溶接に適しており、自動車、航空宇宙、電子機器、医療産業など、幅広い用途で使用されている。抵抗溶接は、主に鉄鋼やアルミニウムなどの導電性金属材料に適しており、自動車、家電製品、建設業界などで広く使用されている。
正しい溶接方法を選ぶには?
溶接は、欠かすことのできない接合技術として、さまざまな産業で重要な役割を果たしています。しかし、市場には多種多様な溶接方法が出回っており、業界のニーズに最適な溶接技術を選択することは、多くの企業にとって課題となっている。次に 選ぶ お客様の業界に最適な溶接方法を多角的に検討します。
- ワークの材質と厚さ
さまざまな溶接方法は、次のような場合に適している。 違う 材料と厚さに適している。例えば、レーザー溶接は様々な金属や一部の非金属材料に適しており、特に薄板溶接に優れている。対照的に、アーク溶接は は 好適 にとって 厚板溶接と大型構造部品。したがって、溶接方法を選択する際には、まず被加工材の種類と板厚を考慮する必要がある。
- 溶接品質と精度の要件を評価する
業界によって、溶接の品質と精度に対する要求はさまざまである。例えば、航空宇宙や医療機器のような業界は、溶接の品質と精度に対する要求が極めて高く、レーザー溶接や電子ビーム溶接が理想的な選択肢となる。一方、建設や橋梁のような業界は、溶接の品質と精度に対する要求が比較的低く、アーク溶接や抵抗溶接のような従来の溶接方法でもニーズを満たすことができる。
- 生産効率とコスト重視
溶接方法の選択は、生産効率とコストも考慮する必要がある。高度に自動化された 溶接 レーザー溶接や電子ビーム溶接のような方法は、設備コストは高いが、生産効率が高く、大量生産に適している。アーク溶接や抵抗溶接のような伝統的な溶接法は、設備コストは低いが、生産効率が相対的に低く、大量生産に適している。 ふさわしい 小・中規模のバッチ生産または現場溶接用。
- 環境要因と安全性を考慮する
溶接方法によっては、溶接工程中にヒューム、 有害ガス、放射線を発生させ、環境や作業者の 健康に影響を与えるものもある。そのため、溶接法を選択する際には、環境要因と 安全性も考慮する必要がある。レーザー溶接と電子ビーム溶接は比較的環境に優しいが、アーク溶接は保護措置に注意が必要である。
- 専門家のアドバイスを求める
もしあなたが 知らない 溶接技術に精通していない、あるいは自分の業種 に最も適した溶接方法を判断するのが難しい場 合、専門家の助言を求めることができる。溶接機メーカーと綿密な打ち合わせを行い、溶接の専門知識について学び、専門的な指導や提案を受けることができる。また、溶接機を購入したことのある友人に、使用経験について尋ねることもできる。
ファイバーレーザー溶接機の選択
ファイバーレーザー溶接機には、ハンドヘルドレーザー溶接機、卓上レーザー溶接機、自動ロボットレーザー溶接機など様々な種類があります。以下は、ファイバーレーザー溶接機のさまざまなタイプの紹介であり、あなたのニーズに基づいて選択することができます。
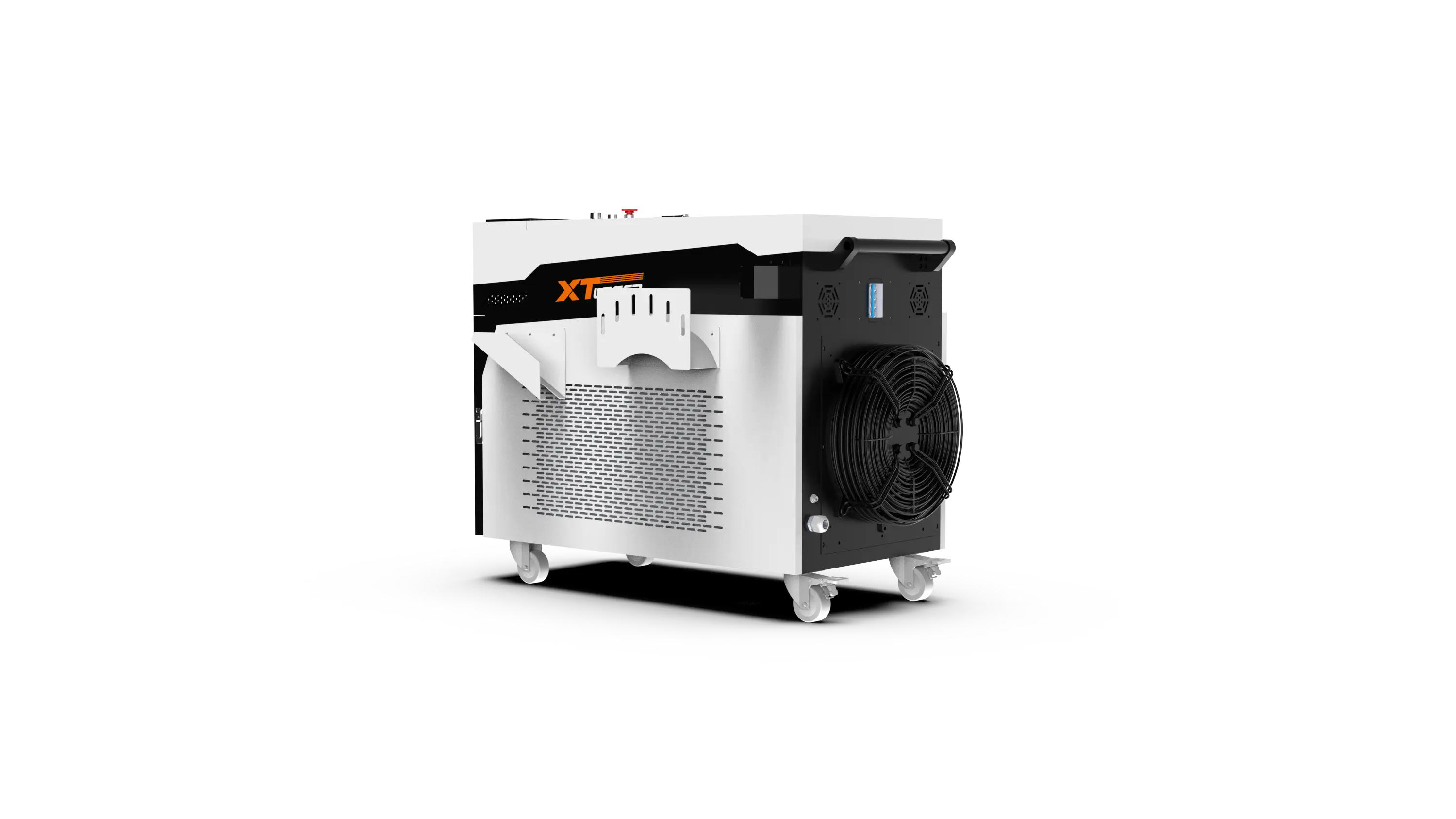
ハンドヘルドレーザー溶接機
1000W/1500W/3000Wオプションあり; スポット/サークル/ライン/その他8種類の溶接モード; 溶接溶け込み深さ 3mm/4mm/5mm

卓上レーザー溶接機
1000W/1500W/3000Wオプションあり; 貫通深さ(ステンレス鋼)2.8mm/4mm/5.2mm; 貫通深さ(炭素鋼)2.7mm/4mm/5mm; 貫通深さ(アルミニウム合金)2.2mm/3.3mm/4.2mm

自動ロボットレーザー溶接機
1000W/1500W/3000Wオプションあり; スポット/サークル/ライン/その他8種類の溶接モード
結論
この記事では、レーザー溶接と伝統的な溶接の比較分析を通じて、さまざまな分野でのさまざまな溶接方法の適用特性を見ることができます。溶接方法を選択するとき 必要がある ワークの材質、溶接要件、生産効率、コストなどの要素を総合的に考慮し、レーザー溶接と従来の溶接方法の長所と短所を比較検討し、特定のニーズに最も適した溶接技術を選択する。
レーザー技術の絶え間ない発展とコスト削減により、レーザー溶接の応用展望はさらに広くなる。より多くの分野で独自の優位性を発揮し、溶接技術の進歩を牽引することが期待される。