Häufige Probleme und Lösungen im Laserschneidprozess
Das Laserschneiden ist eine hochpräzise, hocheffiziente Bearbeitungstechnologie, aber in der Praxis treten unweigerlich einige allgemeine Probleme auf. XT LASER wird die Ursachen dieser Probleme im Detail analysieren und entsprechende Lösungen anbieten, um Ihnen zu helfen, die Schnittqualität effektiv zu verbessern.
Raue Schnittkanten oder Grate
- Analyse der Ursachen
① Unzureichende Laserleistung: Die Leistung ist zu gering, das Material kann nicht vollständig geschmolzen werden, was zu rauen Schnittkanten führt.
② Die Schneidgeschwindigkeit ist zu hoch: Der Laserstrahl bleibt nicht lange genug auf der Oberfläche des Materials, die Bildung von Grate.
③ Brennweite ist nicht korrekt: Die Laserfokusposition ist nicht genau, was die Schnittqualität beeinträchtigt.
④ Falscher Gasdruck: Zu geringer oder zu hoher Druck des Hilfsgases führt zu Gratbildung.
⑤ Unangepasste Materialeigenschaften: Die Schnittparameter sind nicht an die Art und Dicke des Materials angepasst.
⑥ Verschmutzung des Laserkopfes: Schmutz oder Koks auf dem Laserkopf beeinträchtigt die Qualität des Laserstrahls.
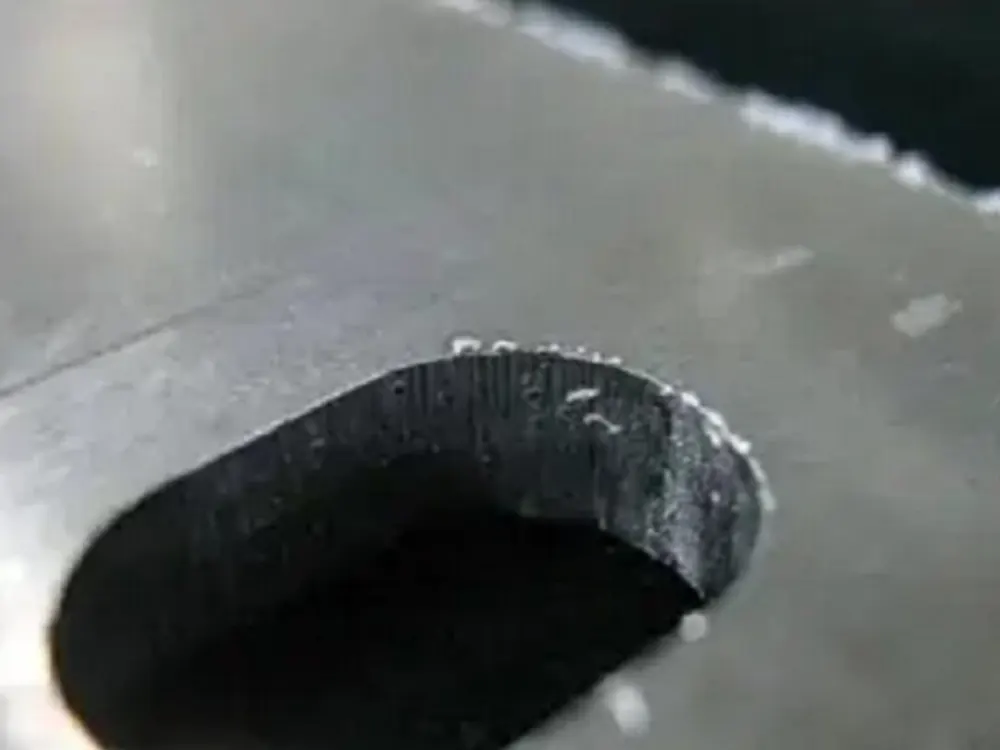
- Lösung:
① Anpassen der Laserleistung: Erhöhen Sie die Laserleistung entsprechend.
① Stellen Sie die Laserleistung ein: Erhöhen Sie die Leistung entsprechend, um sicherzustellen, dass das Material vollständig geschmolzen wird.
② Optimieren Sie die Schnittgeschwindigkeit: Verringern Sie die Geschwindigkeit, damit der Laser genügend Zeit hat, den Schnitt zu beenden.
③ Kalibrieren Sie den Fokus: Vergewissern Sie sich, dass der Laserfokus genau ist und die Fokusposition auf oder leicht unter der Oberfläche des Materials liegt.
④ Stellen Sie den Gasdruck ein: Stellen Sie den Hilfsgasdruck entsprechend den Materialeigenschaften ein und stellen Sie sicher, dass die Durchflussrate stabil ist.
⑤ Wählen Sie geeignete Parameter: Machen Sie sich mit den Materialeigenschaften vertraut und stellen Sie die Schneidleistung und -geschwindigkeit angemessen ein.
⑥ Reinigen Sie den Laserkopf: Reinigen Sie den Laserkopf regelmäßig, um das Gerät in gutem Zustand zu halten.
Der Schnittbereich ist zu breit oder es kommt zu Schmelzvorgängen
- Analyse der Ursachen
① Laserleistung ist zu hoch: Die Leistungseinstellung ist zu hoch, was zu einem übermäßigen Schmelzen des Materials führt.
② Die Schneidgeschwindigkeit ist zu langsam: zu langsam, damit der Laser zu lange verweilt und die Wärmeeinflusszone vergrößert.
③ Ungenauigkeit der Brennweite: Falsche Position des Brennpunkts, was zu einer Vergrößerung des Durchmessers des Laserstrahls führt.
④ unzureichender Hilfsgasstrom: Ein unzureichender Gasstrom kann das geschmolzene Metall nicht wegblasen und verschlimmert das Schmelzphänomen.
⑤ Die Materialeigenschaften sind nicht geeignet: Bestimmte Materialien oder Materialien mit größerer Dicke sind eher zum Schmelzen geeignet.
⑥ Schlechte Laserstrahlqualität: Eine schlechte Gleichmäßigkeit des Laserstrahls oder ein schlechter Divergenzwinkel beeinträchtigen die Schneidwirkung.
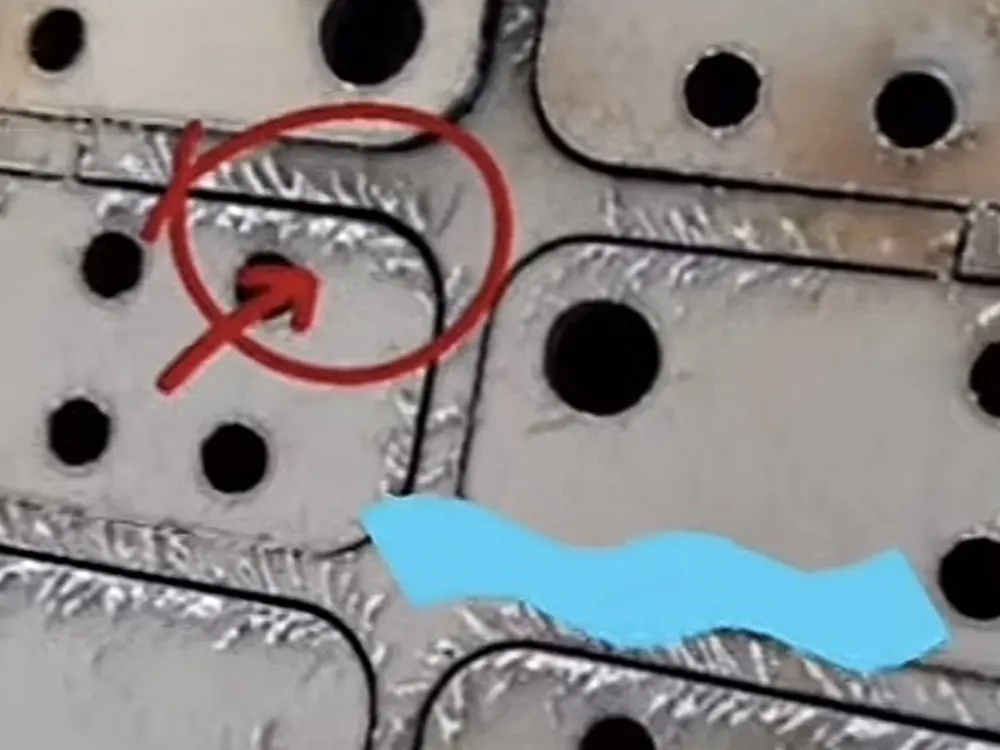
- Lösung
① Reduzieren Sie die Laserleistung: je nach Materialeigenschaften der entsprechenden Reduzierung der Laserleistung.
② Schnittgeschwindigkeit erhöhen: Passen Sie die Geschwindigkeit an, um Schmelzprobleme zu vermeiden, die durch zu langsames Schneiden verursacht werden.
Kalibrieren Sie die Brennweite: Stellen Sie sicher, dass die Laserfokusposition korrekt ist.
④ Erhöhen Sie den Hilfsgasstrom: Stellen Sie sicher, dass der Gasstrom ausreicht, um das geschmolzene Metall wirksam abzublasen.
⑤ Wählen Sie das richtige Material und die richtigen Parameter: Stellen Sie vor dem Schneiden die Parameter angemessen auf die Materialeigenschaften ein.
⑥ Verbessern Sie die Qualität des Laserstrahls: Warten Sie die Laserausrüstung regelmäßig, um die Qualität des Laserstrahls zu gewährleisten.
Die Schnittfläche ist nicht eben und weist Wellen auf.
- Analyse der Ursachen
① Fluktuation der Laserleistung: Die instabile Laserleistung führt zu einer ungleichmäßigen Energieverteilung.
② Schneidgeschwindigkeit ist nicht einheitlich: Geschwindigkeitsänderungen beeinflussen die Laserstrahl auf der Oberfläche des Materials Zeit.
③ Brennweitenungenauigkeit: falsche Lage des Brennpunkts, Abnahme der Schnittqualität.
④ Materialverformung oder Unebenheiten: Materialverwerfungen oder Oberflächenunebenheiten beeinträchtigen die Schneidwirkung.
⑤ Vibration des Laserkopfes: Die mangelnde mechanische Stabilität des Geräts kann zu Vibrationen führen.
⑥ Instabiler Hilfsgasstrom: Ein instabiler Gasstrom beeinträchtigt die Blaswirkung von geschmolzenem Metall.

- Lösung
① Stabilisierung der Laserleistung: Stellen Sie eine angemessene maximale und minimale Leistung ein, um eine stabile Laserleistung zu gewährleisten.
② Optimieren Sie die Schnittgeschwindigkeit: Halten Sie die Geschwindigkeit konstant und vermeiden Sie Geschwindigkeitsschwankungen beim Schneiden.
③ Kalibrieren Sie den Fokus: Passen Sie die Laserfokusposition regelmäßig an, um die Schnittgenauigkeit zu gewährleisten.
④ Prüfen Sie die Ebenheit des Materials: Richten Sie das Material vor dem Schneiden gerade, um eine Beeinträchtigung der Schnittqualität durch Verziehen zu vermeiden.
⑤ Verbessern Sie die Stabilität des Laserkopfes: Prüfen Sie die mechanischen Teile des Laserkopfes und ziehen Sie sie fest, um Vibrationen zu reduzieren.
⑥ Gasfluss kontrollieren: Stellen Sie sicher, dass der Hilfsgasstrom stabil ist, um die Qualität der Schnittfläche zu verbessern.
Ungewöhnliche Funkenbildung beim Schneiden
- Analyse der Ursachen
① Zu hohe Laserleistung: Eine zu hohe Einstellung der Laserleistung kann zu einem übermäßigen Schmelzen des Materials führen und eine große Anzahl von Funken erzeugen.
② zu langsame Schnittgeschwindigkeit: Bei zu langsamer Schnittgeschwindigkeit verbleibt der Laser zu lange auf dem Material, was die Funkenbildung erhöht.
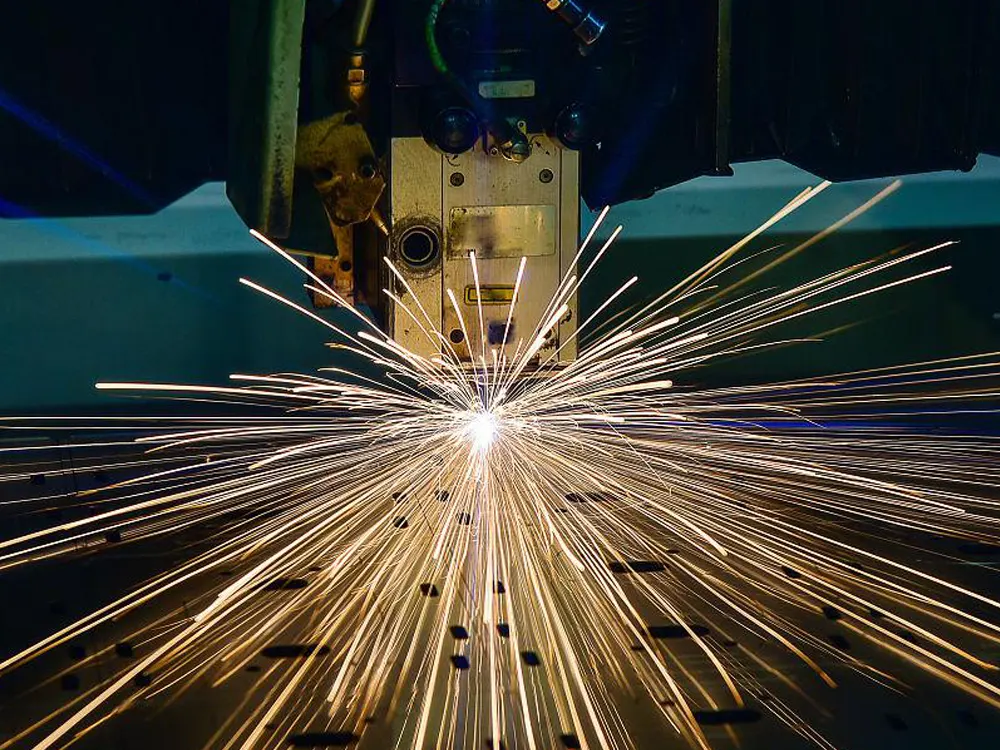
- Lösung
① Passen Sie die Laserleistung an: Reduzieren Sie die Laserleistung entsprechend der Dicke und Art des Materials, um die Funkenbildung zu verringern.
② Optimieren Sie die Schneidgeschwindigkeit: Erhöhen Sie die Schneidgeschwindigkeit, um sicherzustellen, dass der Laser für eine angemessene Zeit auf das Material einwirkt, um Funkenbildung durch zu langsames Schneiden zu vermeiden.
Qualitätsprobleme beim Laserschneiden sind in der Regel auf Parametereinstellungen, Materialeigenschaften oder unzureichende Wartung der Anlagen zurückzuführen. Durch Anpassung von Leistung, Geschwindigkeit, Brennweite und Optimierung des Hilfsgasflusses usw. kann die Schnittqualität wirksam verbessert werden.